These permit a change in direction of piping, a change in size of pipe, or a branch to be made from the main run of pipe. These are Elbows, Tees, Reducers, Caps. They are formed from plate or pipe, machined from forged blanks, cast, or
molded from plastics.
Screwed or socket-welding forged steel fittings are rated to the nominal cold non-shock working pressure of 2000, 3000 and 6000# (PSI).
Branching
There are different methods of branching. These are done by Stub-In, Weldolet, Elbolet, Latrolet, Sweepolet, Cross, Lateral, Shaped Nipple, Nipples.
Tees
Butt Weld Tee: Straight and Reducing: These are used for making 90
o branching from the main run of pipe. Straight tees with a branch of same size as pipe, are readily available. Reducing tees have branch smaller than the size of the pipe. These are not readily available. Tees do not require reinforcing.
Stub-In: It is the term used for a branch of pipe welded directly into the side of a main run of pipe. It is not a fitting. This is the commonest and least expensive method of welding a full size or reducing branch for pipe of size 50 mm NB and larger. A stub-in can be reinforced.
Weldolet: It makes a 90
o branch, of full size or reducing on straight pipe. Closer manifolding is possible than with tees. Flat based weldolets are available for connecting to pipe caps and vessel heads. You need to specify 2 sizes for branching on pipe.
Elbolet: It makes a reducing tangent branch on long radius and short radius elbow. You need to specify 2 sizes for branching.
Latrolet: It makes a 45
o reducing branch on a straight pipe. You need to specify 2 sizes for branching.
Sweepolet: It makes a 90
o reducing branch from the main run of pipe. It is primarily developed for high yield pipe used in Oil & Gas transmission lines. It provides good flow pattern, and optimum stress distribution. You need to specify 2 sizes for branching.
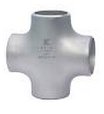
Cross Straight or Reducing: Straight crosses are usually stock items. Reducing crosses may not be readily available. For economy, availability and to
minimize the number of items in inventory, it is preferred to use tees and reducers, and not crosses, except where space is restricted, as in marine piping or revamp work. Reinforcement is not needed for these.
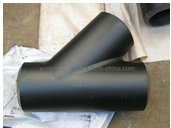
Lateral Straight or Reducing: It permits odd-angled entry into the run of the pipe, where low resistance to flow is
important. Straight laterals with branch bore equal to run bore are available in Standard and XS weights. Reducing laterals and laterals at angles other than 45
o are usually available only to special order. Reinforcement is required where it is necessary to restore the strength of the joint, to the full strength of the pipe.
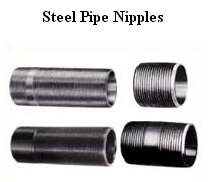
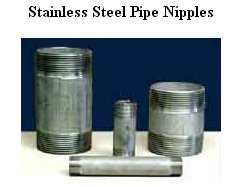
Nipples: These join unions, valves, strainers, fittings etc. Basically it is a short length of pipe either fully threaded (close nipple) or threaded at both ends (TBE), or plain one end and threaded one end (PEO-TOE). These are available in various lengths. Nipples can have grooved ends also.
Shaped Nipple: These are rarely used, but can be used for branching at 90
o and 45
o or at any other angle. The run pipe is field cut using nipple as template. It needs reinforcement if it is necessary to bring the strength of the joint upto the full strength of the pipe.
Hose to pipe connectors: These are used to join a pipe to hose. Hose is flared on the end.
Tank Nipple: It is used for making a screwed connection to a non pressure vessel or tank in low pressure service. Overall length is usually 150 mm, with a standard taper pipe thread at each end. On one end, the taper pipe thread runs into a ANSI lock nut thread.
Elbows
These are of following types. Long Radius and Short Radius Elbows, Reducing Elbows, Long Radius Tangent Elbow, Returns, Bends and Mitered Elbows.
Long Radius and Short Radius Elbows: These make 90
o and 45
o change in direction of the run of pipe. The elbows normally used are Long Radius (LR) with centerline radius of curvature equal to 1.5 times the nominal pipe size (NB) for 20 NB and larger sizes. Short Radius (SR) elbows with centerline radius of curvature equal to the nominal pipe size (NB) are also available.
Long Radius Tangent Elbow: These are special elbows that provide a straight length at the end to acomodate a slip on flange. It is 90
o long radius elbow with a straight extension at one end (Long Tangent).
Reducing Elbows: These are designed both to change direction and reduce pipe size. These have centerline radius of 1.5 times the nominal size of larger end. Their use eliminates one fitting (reducer) and reduces welding by one third. The gradual reduction in diameter through the arc of reducing elbow provides maximum flow efficiently, reduces turbulence and erosion and helps in maintaining pressure.
Return: It changes the flow of direction in 180
o and is used to make heating coils, vents on tanks etc.
Bends: These are made from straight pipe. Common bending radii are 3 and 5 times the pipe size (NB). Bends with larger radius can be made by hot bending. Only seamless or ERW pipe is used for bends.
Mitered Elbows: These are fabricated as required from the pipe of the same NB and these are not fittings. The miters are used for pipes with NB 200 and larger where pressure drop is not important and regular elbows are costlier. A 2-piece 90
o miter has 4 to 6 times hydraulic resistance of the corresponding long radius elbow. A 3-piece 90
o miter has about double the resistance. 3, 4 and 5-piece miters are normally used.
Reducers
Reducers are used to change the size of the pipeline. These are of two types.
Concentric Reducers: The centerline of inlet and outlet is at same level. It is generally used in vertical pipes and in lines where flow pattern is critical, near flow instruments or control valves.
Eccentric Reducers: The eccentric reducer is used when it is necessary to keep either the top or bottom of the line at one level. These are used with flat side up or down. Flat side down is used in horizontal pipes. This helps in maintaining level of bottom of pipe at the same level after reduction of pipe size. Flat side up is used for pump suction line so that all air trapped in suction line is removed to pump.
Sizes of Reducers: Reducers are available in fixed sizes. Smaller size can be up to half of higher size with one lower size. Length of all these is same.
- 100 x 90 or 4” x 3 1/2”
- 100 x 80 or 4” x 3”
- 100 x 65 or 4” x 2 1/2”
- 100 x 50 or 4” x 2”
- 100 x 40 or 4” x 1 1/2”
Swage
Swage is used
- To connect butt weld pipe or fitting to smaller screwed or socket weld pipe or fitting.
- In butt weld pipes it is used when greater reduction is required (Instead of two reducers).
These are of three types. Concentric, eccentric and ventury type.
Concentric Swage: The centerline of inlet and outlet is at same level. It is generally used in vertical pipes.
Eccentric Swage: The eccentric swage is used when it is necessary to keep either the top or bottom of the line level. These are used with flat side up or down. Flat side down is used in
horizontal pipes. Flat side up is used for pump suction line.
Ventury: Ventury type swage gives a smooth flow. This is used in pipe on either side of a control valve.
Cap
Caps are used to seal the end of pipe. These are flat or ellipsoidal in nature.
Flat Closure: These are flat plates normally cut from plate at site.
Dished Heads: These are used to close large diameter pipes. These can also be used for small diameter pipes especially in condensate drip leg. Welding is very good and has high strength. These can be easily cut open in future.
Socket Weld Fittings
These are used to connect small bore pipe (up to 40 NB). Fittings are also available up to 80 NB in US, for use in exceptional cases. These have fillet weld on socket weld end. Weld does not intrude in pipe, which is very essential for small bore pipes.
Full Coupling: It is also termed as coupling and it joins one pipe to another pipe, or to nipple, swage etc. This is of forged type or prepared from bar stock.
Half Coupling: It is used to make side branching on large diameter pipes or vessels. It is of the same length of full coupling but has socket weld end on only one side. Shaping is necessary for the flat end to suit curvature of pipe or vessel. This is of forged type or prepared from bar stock.
Reducer: It joins two pipes with different NB. Bores on either side are in same line but are of different sizes. This is of forged type or prepared from bar stock.
Cross: These are used in exceptional cases where two tees cannot be fitted. Mostly used in marine piping or during modifications.
Sockolet: It makes a 90o branch, either full size or reducing on a straight pipe. Socket weld end is on smaller end. You need to specify 2 sizes.
Elbolet: It makes a reducing tangent branch on elbows. You need to specify 2 sizes.
Swaged Nipple: It is similar to swage. These can allow two types of joining. Socket ended items of different sizes which has plain ends on either sides for insertion into socket ends. A socket ended item to a larger butt welding pipe or fitting. This type has larger butt-weld end and smaller socket weld end.
Elbows: These change pipe direction in 90o and 45o from the run of the pipe. The ends are socket weld type.
- Latrolet: It makes a 45o reducing branch on straight pipe.
- Nipolet: A varient of sockolet, having integral plain nipples. Primarily developed for small valved connections.
- Stub In: Not recommended for pipes with diameter less than 50 mm, due to risk of weld material entering line and restricting flow.
- Lateral: It makes full size 45o branch from the main run of the pipe.
Screwed Fittings
These are used to connect pipes or fittings with screwed ends. These are more common in Galvanized Iron pipes and fittings for plumbing operations.
Full Coupling: It is also termed as coupling and it joins a pipe or fitting to another with threaded ends.
Half Coupling: It is used to make 90o screwed connections for pipes to instruments, or for vessel nozzles. Welding heat may cause embrittlement of the threads of this short fitting.
Reducer or Reducing Coupling: It joins threaded pipes with different diameters. Can be made in any reduction by boring and tapping standard forged blanks.
Cross: These are used in exceptional cases where two tees can not be fitted. Mostly used in marine piping or during modifications.
Threadolet: It makes a 90o branch, full size or reducing on a straight pipe. You need to specify 2 sizes.
Elbolet: It makes a reducing tangent branch on elbows. You need to specify 2 sizes.
Nipples: These join unions, valves, strainers, fittings etc., It is basically a short length pipe with screwed ends.
Swaged Nipple: It is similar to swage. These can allow two types of joining. Screwed items of different sizes which has screwed ends on either sides. A screwed item to a larger butt welding pipe or fitting or vice versa.
Elbows: These change direction of pipe in 90o and 45o from the run of the pipe. The ends are threaded internally.
Threaded Flange: This is similar to slip on flange, but has internal threads.
Latrolet: It makes a 45o reducing branch on straight pipe. It is welded on pipe.
Nipolet: A varient of threadolet, having integral plain nipples. Primarily developed for small valved connections.
Stub In: Not recommended for pipes with diameter less than 50 mm, due to risk of weld material entering line and restricting flow.
Bar Stock Plug: It seals the screwed end of a fitting. Also termed as round head plug.
Flanges
These are used for pipe connections that can be easily opened and are of following types. Weld Neck, Slip On, Reducing, Lap Joint and Blind.
Weld Neck Flange, Regular and Long: Regular weld neck flanges are used with butt-weld fittings and pipes with bevelled ends. Long weld neck flanges are primarily used for vessel and equipment nozzles, and rarely for pipe. These are suitable where extreme temperatures, shear, impact and vibratory stresses apply. Regularity of bore is maintained in this. Mostly used in pipe lines having high pressure and temperature.
Slip On Flange: It is generally used to connect two pipes. Slip-on flanges can be used with long-tangent elbows and swages without any pipe between them. The internal weld is slightly more subject to corrosion than butt-weld. The flange has poor resistance to shock and vibration. It introduces irregularity in the bore, if not welded properly. It is cheaper than weld neck flange to buy, but is costlier to assemble. It is easier to align compared to weld neck flange. Calculated strengths under internal pressure are about one third that of corresponding weld neck flange. Pipe or fitting is set back from the face of flange a distance equal to wall thickness.
Reducing Flange: It is suitable for changing size, but should not be used if abrupt transition would create turbulence, as at pump connections. Available to order in weld neck type and from stock in slip-on types.
Expander Flange: It is similar to weld neck flange but increases size of pipe to first or second larger size. It is alternative to using reducer and weld neck flange. Useful for connecting to valves, compressors, and pumps. Pressure ratings and dimensions are in accord with ASME/ANSI B16.5.
Lap Joint Flange: It is economical if the pipe used is of costly material such as stainless steel. As the flange can be carbon steel and only the lap joint stub end need to be of line material. A stub end must be used in a lap joint, and the cost of two items must be considered. It is also useful where alignment of bolt holes is difficult, such as with spools to be attached to flanged nozzles of vessels.
Blind Flange: It is used to blind off a flange, generally at the end of a pipe. This provides an easy way to open the end of a pipe for further running of the pipe.
Bolt Holes in Flanges are even in number and are equally spaced. These are straddled vertically. ASME/ANSI B16.5 specifies the number of bolt holes, diameter of bolt circle and diameter of bolt holes. Number of bolts, size of bolt holes and size of bolts (diameter and length) are different as per rating of the flange.
Flange Facing: Many facings for flanges are offered by manufacturers, including various tongue and groove types which must be used in pairs. However only four types of facing are widely used. The raised face is used for 80% of all flanges. The ring-joint facing, employed with either an oval-section or octagon section gasket, is used mainly in Petrochemical Industry.
The four types of faces are as follows:
Raised Face: It has a raised face with serration on it to hold the gasket firmly in position. This is widely used.
Flat Face: Most common uses are for mating with non-steel (mostly Cast Iron) flanges on bodies of pumps, valves etc. and for mating with 125# cast-iron valves and fittings. A full size gasket is used to avoid breaking of the flange while tightening.
Ring Joint Facing: It is more expensive facing and used in pairs for high temperature and high pressure service. Both flanges of the pair are alike.
Lap Joint Facing: It has special curvature for accommodating stub end. The combination of flange and stub-end presents similar geometry to the raised face flange and can be used where bending stresses will not occur. This is used for SS pipes, where stub-end is made of SS pipe and flange is made of Carbon Steel.
Flange faces are usually finished by machining to produce a spiral round-bottomed groove, or a V shaped spiral or concentric groove. It is termed as serrated finish. Smooth finish is generally made to order. Serrated finish is used with asbestos and other gaskets. The regular smooth finish is used with gaskets made from harder materials and with spiral wound gaskets.
Flange Finishes: The term finish refers to the type of surface texture produced by machining the flange face which contracts the gasket. Two principal finish types are serrated and smooth.
Gaskets: These are used to make a fluid-resistant seal between two surfaces.
The common gasket patterns for pipe flanges are
- Full-face for use with flat-faced flanges
- Ring type for use with raised face flanges
Widely used materials for gaskets are compressed asbestos (2 and 5 mm thick) and asbestos filled metal. The filled metal gasket is especially useful if maintenance requires repeated uncoupling of flanges, as gasket separates clean and is often reused.
Bolts for flanges: Two types of bolting is available, studbolt using two nuts and the machine bolt using one nut. Studbolts have largely displaced regular bolts for bolting flanged piping joints, as studbolt can be removed easily, confusion with other bolts at site is avoided, the odd sized can be readily made from roundstock. ASME/ANSI B16.5 defines studbolts for all flange classes while it defines machine bolts for class 150# and 300# only.