Distillation Systems / Heat Exchanger Systems
- Vertical Tower: Normally vessel components are described using common terms such as shell, head, nozzle, and support. Some vessels will also have special terms based on function. Typical special terms include the following:
1. Flash Section is the area or zone of the fractionation vessel where the primary feed enters the vessel.
2. Fractionation Section is the portion of the vessel that includes the trays.
3. Stripping Section is a place in the vessel that includes the introduction of supplementary heat such as high temperature steam.
4. Surge Section is the bottom portion of the vessel that normally includes the main outlet nozzle, which is connected to the bottom pumps.
- Common problems with vertical vessels: Most important is schedule crunch. Vessels scheduled for purchase too early, requiring firm orientations with very little backup information. The information required is approved and issued documents for Design, such as Piping & Instrumentation Diadram, Exchanger type and location, flare header and location of pressure safety valves. Thin wall vessels not able to support load of pipe supports. High wind presence requires extra guides. Late changes to pressure safety valve sizing, prompts changes to pipe support and guides on line to flare. Late change to control valve location criteria, due to which flashing services are required to be located to elevated platform on vessel, with line downstream of valve self draining to vessel. Reboilers requiring spring mounted supports have to be moved due to tight piping and differential growth. High steam outlet temperature requires extra flexibility in the piping. Extra heavy object removal is difficult if there is increase in excess load of Davit.
- Vertical Vessel Orientation: The ladder approach at grade should be free of obstructions and easily accessible. Verify preferred location with Project requirements. The Manhole orientation should be oriented in the back half of the vessel toward the access way. The manholes should be arranged with consideration to the type of load handling device. You should maintain one centerline if monorail is used, one or two centerlines if davit is used, no specific restriction if crane is used. Load drop area should be located on the main access side. Level instruments should be located on or near the front half of the vessel and visible from the main operating aisle. The piping risers to and from the vessel should be located to the front half of the vessel for easy routing to the pipe way and equipment.
- Manholes: Manholes will influence the entire vessel orientation to a certain degree. The location of the manholes must be compatible with the location of the tray down comers. The down comers in turn influence the location of the piping and instrument nozzles. The preferred elevation of manholes, above the platform is 2 feet 6 inches, from the centerline. The limits are minimum 6 inches from the top of the platform to the bottom of the flange, or maximum 4 feet from the top of the platform to the bottom of the flange. Verify preferred location with Project requirements. Platforms may not be required for manholes that are 15 feet or less above grade, unless a platform is required for another reason such as an instrument. Verify preferred location with Project requirements. Space and clearances are important around manholes. Check flange swing and tray lay down space.
- Ladders and Platforms: Check to see that the approach to the ladder at grade is clear of all obstructions and hazards, the entry onto each platform is clear and not blocked by level or other instruments, the entry onto each platform is clear and not blocked by an open manhole flange, there is a clear path from one down ladder to the next down ladder for unobstructed travel during emergencies. Platforms may need to be added or extended for access to operating valves, spectacle blinds, or instruments. Special platforms are often required at the channel end of a thermo-siphon reboiler or other equipment that is mounted directly into or onto the vessel. Investigate lining up and connecting platforms servicing equipment, such as Reboilers or Accumulators, which are located in adjacent structures but related to the vessel. Maintenance criteria at Reactors often require platforms large enough and strong enough for large flange or head lay down in addition to catalyst storage and handling. Check the location and size of the pipe penetration holes through platforms. The opening is to be one inch larger in diameter than the flange or pipe plus insulation, which ever is greater. Provide proper routing and support for all lines regardless of size. Do not route small lines vertically behind the ladders. Do not route small lines vertically between the vessel shell and the inside radius of the platforms. Do not route small lines vertically up the outside of the platforms in line with or close to the manholes. Ladder access openings must be fitted with a safety gate. Check for proper clearance for gate swing. Some processes are subject to periods of hazardous operations. Ladders and ladder cages may need to be designed for operators with self-contained suits and air packs.
- Reboilers: Reboilers will be either Fired or Heater Type, Thermosiphon which can be vertical or horizontal shell & tube type, or Kettle type which can be horizontal shell & tube type. Fired Reboilers shall be located a minimum of fifty feet from the vessel. Piping to and from any type of reboiler will be hot, and have sensitive flow conditions. The Kettle or Thermosiphon Reboiler elevation is set by Process and indicated on the Piping & Instrumentation Diadram.
- Pipe Supports and Guides: Piping is responsible for locating the pipe supports and guides on vessels and for defining the size and loads on the pipe supports on vessels.
- Piping Flexibility: Piping must determine the operating thermal growth of the vessel. The vessel will have a series of temperature zones from the bottom to the top. The differential expansion between the piping risers and the vessel must be checked to prevent over stressing the piping or the vessel shell. The routing of cooler reflux lines must consider the total growth of the hotter vessel. Potential for differential settlement needs to be investigated. Each piping system or line needs to be considered individually.
- Instrumentation: The high and low level alarms need to be carefully considered because they will set the elevations of the level instruments. Orientation of level instrument connections needs to consider the internals. All instruments shall be accessible. Watch out for space requirements for gage glass illuminators. Temperature indicators and thermowell connections will require removal space.
- Electrical: Space shall be allocated for conduit runs up the vessel. These conduits will carry power to platform lights, gage glass illuminators, and in some cases electrical tracing. Conduits are also required for controls and for instrumentation cables.
- Piping Valves: Valves are meant to be operated. To operate them, they must be accessible. 2 inch and smaller valves may be considered accessible from a platform or ladder. 3 inch and larger valves shall be accessible on a platform.
- Miscellaneous Piping issues: Lines to and from vessels may be subject to conditions such as 2 phase flow or vacuum. Some Pressure Safety Valves relieving to atmosphere will require snuffing steam. The steam pressure in the line must be adequate to reach the top of the vessel. Large overhead lines verses location of Pressure Safety Valves, require special attention for function and support. Vertical vessel piping needs to be checked for heat tracing requirements. A tracer supply manifold may need to be added at the top of the vessel.
- Ease in Construction: All vertical vessels shall be reviewed for ease in construction. This review needs to consider receiving logistics, lay down orientation, lifting plan, pre-lift assembly items. Pre-lift assembly items may include Piping, Platforms, Ladders, Internals, Paint, Insulation.
- Fire Protection: Some vessels may require special insulation for fire protection, fire monitor coverage and sprinkler systems.
- The other Components include the following:
- Trays: The type of trays, the number of trays, and the number of passes are not the specific responsibility of the piping layout designer. However, there is the need to know about it. A common understanding of terminology will improve communications and prevent errors. The common tray parts are
- Tray support Ring: The tray support ring or Tray ledge is technically not a part of the tray itself. The tray support ring is only there to support the tray. If there are no trays, then there is no need for tray support rings, therefore tray rings are linked to the trays. Tray support rings are normally a simple donut shaped strip welded to the inside of the vessel. They could also be in the shape of an inverted L welded to the vessel wall. Problems arise when the Designer does not allow for the tray support device.
- Tray Deck: One or more sections, consisting of plates, form a horizontal obstruction throughout all or part of the vessel cross section. The trays will normally be constructed to form one or more flow patterns called passes. The purpose of tray deck is to provide a flow path for the process commodity and contain the fractionation or separation device.
1. A Weir is a low dam on a tray to maintain a liquid level on the tray.
Down comer is the primary liquid passage area from higher tray to another lower tray.
3. Valves are also tray hardware devices.
4. Bubble Caps is another tray hardware device.
5. Draw off is a way to remove liquid from the vessel.
6. Trough is a way to collect and move liquid from one point to another.
7. Riser is a device to channel vapor from one lower point to a higher point.
8. Seal Pan is a device with a liquid seal that prevents vapors from passing.
9. Beams & Trestles is a devices that support trays or other types of internals in very large diameter vessels.
10. Baffles is a separation device inside a vessel.
 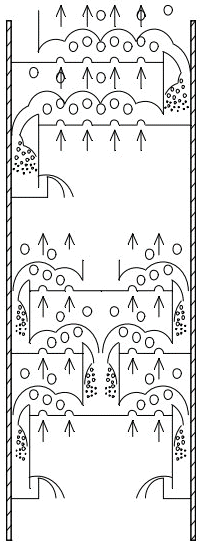 Tray Pass Patterns: The trays and the related downcomers can be arranged in a wide verity of patterns. Typical Tray arrangement, is Single Pass which is quite common. This tray pass arrangement has one feed point, one flow direction, and one downcomer. The single pass tray will normally be used on small diameter vessels and the smaller diameter of a Coke Bottle vessel. Cross-Flow and Multiple Pass trays come in two pass, three pass, four pass, and on and on. These will normally be found in the larger diameter vessels. Multiple pass trays require multiple feed and draw off arrangements. The more passes, the more complex the orientation problems. Reverse Flow or Single Pass, Radial Flow, Circumferential Flow, Cascade Flow are rare. The single pass tray will have a single down comer. The 2, 3, or 4 pass tray will have the same number of down comers as passes. The number of passes and number of down comers, will have a big effect on the orientation. Some towers may have more than one Tray pass configuration. They may have single pass in the top Trays and two-pass Trays in the bottom. The change from one pass configuration to another is chance for error. The alignment of the single pass tray will normally be perpendicular to the two pass trays.
- Tray Types: There is what would be considered Standard Trays, and there are also high efficiency trays.
1. Standard Trays have an open down comer with no separation occurring in the down comer area. This tray is the old stand-by and has been used for many years.
2. High Efficiency Trays have a sealed downcomer with separation occurring in the down comer. This tray type is fairly new. It will most likely be used on most new vessels in the future. It is also the type of tray that is favored on revamp projects to get more out of an existing tower.
- Tray hardware devices: The normal trays inside the typical vertical vessel will contain openings or holes and may be fitted with a fractionation or separation device. This device is what will accomplish the purpose of the vessel. If these devices are not present or do not function properly then the product is not made. There are some common tray devices.
1. Bubble Cap which is used mostly on revamps. Simple, and common method to facilitate the separation process. The Bubble Cap will normally be a round cup shaped cap, inverted over a short and smaller diameter chimney. The skirt area of the inverted cap may be plain or have open or closed slots. Box Cap is very much like the common Bubble Cap, except it is square. Tunnel Cap will be a long narrow rectangular shape. Uniflux Tray is a series of overlapping and interlocking plates. In cross section the Uniflux tray will have the shape of a reclining squared off. The valve tray is common and has small flat metal plates fitted over the holes in the trays. The plate is loose to move up and down, but is retained in position by a clip type device. Vapor pressure under the valve plate causes it to rise and gravity brings it back down. The second common tray, is sieve tray which has holes and nothing else. The hole size is calculated to provide a fragile balance between the liquid head above the tray and the vapor pressure under the tray.
- Column Internal piping:
- Weirs: There may be a number of places where weirs are used. The simple weir to provide proper tray flooding will normally not cause any design problems. There are also some special purpose weirs that may effect the location of nozzles. In most cases the existence of special purpose weirs will not be known at the start of the Vessel orientation activity.
- Downcomers: Downcomers can come in a verity of shapes also. They are straight across in the horizontal direction, or they can be bent. They can be straight up and down in the vertical direction, they can be sloped, slanted or tapered, or they can be a combination. These variations will all impact the orientation to some extent. The major impact, by the downcomer on the orientation, is the geometry or location of the vertical plane itself. The orientation of the downcomers, will have a direct relationship to the orientation of certain nozzles and manholes.
- Other Tray Terms: Some other terms that will be found relating to trays.
1. Sump is a sealed downcomer type area, that is designed to provide a retention volume for some purpose.
2. Seal Pans is a portion of a tray that is set deeper than the rest of the tray to form a seal for the down comer from the tray above.
3. Side Draw Tray is an arrangement that allows the removal of a specific liquid product.
4. Chimney Tray is a full circumference tray fitted with long open pipes to allow vapor to pass from below the tray to the space above.
5. Baffles are plates installed in the vessel for a specific purpose.
6. Impingement Plates are somewhat like a baffle but normally a plate installed in the vessel at the inlet, to prevent blowout to devices located on the opposite side of the vessel.
7. Tray manholes are there in most, if not all, trays, where it will have a removable panel somewhere in the tray, to allow inspection passage without dismantling the total tray.
- Vessel Support: There is a wide variety in the methods used to support vessels. Each of these support types, may also have variations. The tall towers are generally supported by skirts. Horizontal storage tanks are supported by integral steel saddles. Reactors are supported on lugs. Receivers and feed tanks are supported on legs or are portable on casters. Pads are welded on vessels which are supported on concrete saddles. Direct bury method is used for underground tanks. The method of vessel support depends on various factors. These factors include: process function, operation access, maintenance clearances, ease of constructability, and cost. Meeting the positive criteria for all or the majority of these factors will drive the support method. Each of these vessel support methods has their own good points and bad points. The Tall Skirt is the most common because it meets more of the preferred criteria than the others do. The primary methods of support are Skirts. Tall Skirt on foundation at grade are most common. Short Skirt are on elevated pier foundation, table support, or structure. The minimum height of the skirt is normally set by process based on the Net Positive Suction Head requirements of the pumps or for the reboiler's hydraulic requirements. The designer may need to increase the skirt height due to vertical distance required by pump suction line geometry, Vertical distance required by reboiler line geometry, Operator aisle headroom clearance, and suction line entering the pipe rack without pockets. The approval of the Process engineer, Project Manager, and the Client will be required for any increase to the skirt height. The skirt will have one or more access openings and will have skirt vents. Skirts of vessels in refineries or other plants processing flammable commodities, will normally be fireproofed. The fireproofing is normally a two inch thick layer of a concrete type material applied to the outside of the skirt. Check for the specific type. Some materials may require up to 6 inch to obtain the required fire rating. Legs can be installed on foundation at grade. Lugs on vessels can be put on elevated pier foundation, table support, or structure.
- Load Handling Devices: Load handling devices are required for Vertical Vessels if the vessel is over thirty feet tall or the vessel has removable trays and internals. The vessel has components like Pressure Safety Valves, control valves which require frequent removal for routine maintenance and if the components weigh 100 pounds or more. Davit is a small somewhat inexpensive device used for lifting and supporting heavy objects up and down from elevated platforms but limited to a fixed reach. Monorail is a more expensive method, which is a girder provided along floor ceiling. Crane is a far more expensive method and is dependent on availability. If a davit or monorail is not installed then a crane with the required reach and load rating must be rented or an alternate method must be jury-rigged. Any jury rig method will have a high potential for accident and injury. When a Davit is to be included, the location, swing, the clearance height including lifting device, the reach of the removal items, and maximum load of external items must be determined and furnished. When a Monorail is to be included, the platform, and monorail support configuration, the clearance height including lifting device, the reach to the drop zone, the maximum load of external items where vessels will determine weight of internals, must be determined and furnished to the Vessels engineer.
- Pipe supports and Guides: The Pipe Supports and Pipe Guides for the piping that is attached to the vessel is the responsibility of the Piping Group. You are the Piping engineer and you need to make sure it is properly supported and guided. The rule is that all lines shall be properly supported and guided. One key element of the Pipe Supports and Pipe Guides is the L dimension. The L dimension is the distance from the outer diameter of the back side of the pipe to the outer diameter of the vessel. This dimension should be as small as possible but not less than required for maintenance. The rule of thumb for the L dimension is 12 inches minimum and 20 inches maximum. Dimensions of under the 12 inches and over the 20 inches are sometimes allowed. For example, if fitting make up results in an L dimension of 12 inches, do not add a spool piece and extra weld. Lines should be supported as close to the nozzle as possible. The type of support is based on the weight of what is being supported. It may be just a straight pipe dropping down the side of the vessel, it may be much more. Pipe supports attached to a vessel must be evaluated for the shell thickness, orientation, elevation, the L dimension, the weight of the basic pipe and fittings based on size and wall schedule, the weight of the water during hydro test, the weight of the insulation if any, the weight of any added components such as block valves, control valve stations, relief valves, etc. There should be clearance to other objects like seams, Stiffener rings, Nozzles, Clips, Pipe Lines, Platforms. Pipe supports and guides should be staggered vertically for clearance from supports or guides on other lines running in parallel.
- Platforms, Ladders, and Cages: Platforms with access ladders must be provided as required for access to manholes, operating valves, and instruments as defined in the project criteria. Normally objects below 15 feet from grade will not require permanent platforms and ladders. These objects are judged assessable by portable means. Check the Project design requirements. Platform spacing shall be even foot increments when multiple platforms are serviced from a single ladder. The platforms shall be arranged to allow a minimum 7 feet headroom to underside of any obstruction, minimum 2 feet 6 inches radial width for primary egress path which is inside distance of platform to outside distance of platform, minimum 2 feet 6 inches clear distance between ladders. There should be no obstructions in path between primary egress ladders. Maximum 30 feet vertical travel length of ladder should be between platforms. Side step off at all platforms which is step through ladders, are considered dangerous and therefore should be avoided. This requirement should have been reviewed with the Client and defined in the Design Criteria. Combining with platforms on other vessels when potential for improved operations or maintenance exists. Flanges of top head nozzles shall be extended to provide access to bolts. Minimum 1 foot 6 inches clearance around objects, if for maintenance access only.
- Code Name Plate: Every vessel will have a Code Name Plate. On a vertical vessel the code name plate must be on the pressure containment part of the shell. It cannot be attached to the skirt. The best place for the code name plate on a vertical vessel is 2 feet 6 inches above the horizontal centerline of the surge section manhole. Make sure the location selected is accessible on grade or on a platform.
- Transitions for Coke Bottle Vessels: The cone or transition piece for regular and inverted Coke Bottle vessels may come in the following shapes:
- Flat side: It has a cone, cut from flat plate and formed to a simple cone. There is no knuckle radius at the top or bottom of the cone. The connection to the straight shell of the vessel is an angled weld. Usually there is a reinforcing ring on the shell very close to the shell and cone junction.
- Shaped side: The cone is cut from flat plate and rolled to a shaped cone. There is a knuckle radius at the top and bottom of the cone. The cone has a straight tangent at the top and bottom to match the shells. The connection to the straight shell of the vessel is a common butt weld.
- Lined Vessels: Some vessels will be lined. Linings may be metallic, plastic, or glass. Welding to the vessel shell after initial fabrication is not allowed. Some vessels will have flanged connections that are larger than 24 inches. These connections will occur at connections for piping, reboilers, or other equipment. Flanged connections over 24 inches do not have a single standard and need to be defined for specific type.
- Maintenance Aisles at grade: Equipment maintenance aisle for hydraulic crane with a 12 Ton capacity should have a minimum horizontal clearance width of 10 foot or 3 meters and a minimum vertical clearance of 12 foot or 3.5 meters. Where a fork lift and similar equipment of 5,000 pounds or 2300 kilograms capability, is to be used the minimum horizontal clearance should be 6 foot or 2 meters and the minimum vertical clearance should be 8 foot or 2.5 meters. Where maintenance by portable manual equipment like hand trucks, dollies, portable ladders or similar equipment, is required the minimum horizontal clearance should be 3 foot or 1 meter and the vertical clearance 8 foot or 2.5 meters. Operating Aisle at grade should have a minimum width of 2 foot or 800 millimeters and a headroom of 7 foot or 2.1 meters.
- There are a number of nozzles on a reaction vessel or distillation tower.
- Overhead Vapor Outlet Nozzles: The overhead vapor outlet nozzles on a vertical vessel can have some latitude when it comes to attachment location. The attachment connection can be direct to the top head of the vessel or may be from the side. When the connection is from the side there will normally be a pipe inside the vessel angled up to the top head area. Small vapor outlet nozzles from small diameter vessels can be located outside of the vessel and still be cost effective. Large diameter vapor outlet nozzles on large diameter vessels will be more cost effective, if attached to the top head. The line is then looped over to the selected pipe drop position to go down the vessel.
- Feed Inlet Nozzles: All vertical fractionation vessels will have a feed inlet nozzle. This feed nozzle is special and critical on some vessels. Refinery Crude columns and Vacuum columns are examples that have this type of nozzle. This nozzle installation is characterized by the attached line originated at a fired heater, High temperature, High velocity, Mixed phase flow. It may require internals such as a distributor pipe or impingement plate. A Feed Transfer nozzle will normally be the key nozzle for any large fractionation vessel. Normally any side inlet orientation is possible but in most cases this will then dictate the tray orientation.
- Liquid (secondary) Inlet Nozzles: A normal liquid feed nozzle will not have the same complexities as the Feed Transfer type. This nozzle installation is characterized by the attached line originated at an exchanger, hot but not overly high on the temperature scale, some may have potential for mixed phase flow, normal line velocity. It may require vessel internals such as a distributor or inlet pipe. Watch Instrument connections should be in relationship to Inlets and reboiler returns.
- Reflux Nozzles: A normal reflux nozzle will not have the same complexities as other nozzles. This nozzle installation is characterized by the attached line originated at a pump, low on the temperature scale, all liquid flow and normal line velocity. It may require internals such as a distributor or inlet pipe. Multiple pass trays will require a more complex distributor or inlet pipe than a single pass.
- Draw-Off Nozzles: The purpose of this nozzle is to draw-off or remove the primary product. They are also used to Draw-off a secondary product to side stream stripper. May be installed with a sump to remove unwanted water in the process stream. This nozzle is located in the down-comer area of the column, it may be in a sump. It may be a size larger than the normal attached line size. Some of the initial vertical drop will be the larger size. It should be as per normal line velocity and may require internals if multiple pass trays.
- Bottom Reboiler Feed Nozzles: The liquid outlet nozzle will normally be in the center of the bottom vessel head. This nozzle is located in the bottom of the surge section of the column. It may be of very large size and has normally very low line velocity.
- Side Reboiler Feed Nozzles: This is also a potential Key Nozzle. The liquid outlet nozzle must be oriented in the same quadrant as the bottom down comer. This nozzle is located in the downcomer area of the column and is in a sump. It may be of a larger size than the normal attached line size. Some of the initial vertical drop will be in the larger size. Normally liquid flow in line is at lower velocity. Relationship to elevation of associated reboiler is critical to nozzle elevation and internals.
- Side Reboiler Vapor Return Nozzles: One of the primary issues with this nozzle is the orientation relative to the other internal items and nozzles. If not placed in the right place the velocity of the return can blow liquid out of a seal pan or can affect the readings of any instruments attached to the far wall. This nozzle is attached to the line originated at a thermo-siphon or kettle type reboiler. It has very high temperature, with moderately high velocity. All flow is vapor. It may require internals such as a pipe or impingement plate. Relationship to elevation of associated Reboiler is critical to nozzle elevation and internals.
- Bottoms Out and Drain Nozzles: The bottoms nozzle is normally a source for pump suction. The standard type is located in the bottom head then piped through the skirt with a drain nozzle off the bottom out line nozzle. This would be a combination nozzle. A variation of the bottoms nozzle is the siphon or winter type. This type may be used with the approval of process when bottom clearance is a problem. It is common industry practice to avoid locating any flanged connections inside the vessel support skirt. All flanges are subject to leaks, and vessel skirts are classified as a confined space.
- Level Instrument Nozzles: Extreme care must be used when locating level instrument nozzles. There are access and clearances problems that must be considered on the outside of the vessel. There are sensing location and turbulence problems associated with the inside of the vessel. These nozzles must be attached in the same pressure volume of the vessel. Lower nozzle should be in liquid of the surge section, and upper nozzle should be in vapor space. It should be located in static area or with stilling well. It requires external access for operation and maintenance.
- Pressure Instrument Nozzles: Pressure readings are normally taken in the vapor area of a vessel. Pressure connections shall be located in the top head area, 3 to 6 inches under a tray, or well above any liquid level in bottom section. This nozzle is generally located in vapor space of the vessel. It requires external access for operation and maintenance.
- Temperature Instrument Nozzles: Temperature readings are normally taken in the liquid area of a vessel. Temperature connections shall be located 2 to 3 inches above the top surface of a tray, in the downcomer, or well below any liquid level in bottom section. These nozzles should be located in liquid in the downcomer area. It requires external access for operation and maintenance. It should not interfere with internals. Vapor temperature readings may be required for some situations. When required the preferred location is in the down comer area half way between the two trays. Tangential or Hillside connections may be required due to the thermowell length or to accommodate access from the ladder and platform arrangement. With the Process Engineer's approval, investigate the possibility of raising or lowering the temperature point one tray for better ladder and platform arrangement.
- Steam-Out Nozzles: Process plant vessels that contain hydrocarbon or other volatile fluids or vapors will normally have a Steam Out Nozzle. This nozzle has a number of options. A simple blind flanged valve on the nozzle can be installed after the plant is shut down by Operations. The maintenance group would remove the blind flange from the valve. They then attach a temporary flange fitted with a hose coupling and proceed to steam out the vessel by connecting a hose from a utility station. A blind flanged valve and hard piped steam line configured with a steam block valve and a swing elbow can also be installed. A fully hard piped connection from a steam source can be provided. This method would have double block valves, a bleed, and a spec blind for positive shutoff. The vessel steam out nozzle should be located near the bottom surge section manhole on vertical vessels.
- Manholes: Manholes are also considered a nozzle. They just do not have any pipe attached to them. They are however, a very complex piece of the vessel orientation puzzle. The types of manholes normally relate to the method of cover handling provided. Manholes come in the following types. A Manhole may be hinged for side mount, for top mount, or for bottom mount. A Manhole may have davit for side mount or top mount only. A Plain Manhole may be for side mount, for top mount, or for bottom mount. The manhole orientation in top or non tray section of a vertical vessel is somewhat flexible. Normally any orientation is possible. However, the orientation of the manhole should be checked to insure that the entry path is not blocked by any internals. The Manhole may be located in the top head on large diameter vessels if there is a platform that is required for other items. Top Manholes on large diameter vessels have their built in good points and bad points. The good point is that during shutdown the open manhole provides for better venting. It also allows for a straight method for removal and reinstallation of the trays. The bad point is that ladder access must be provided down to the top tray, and the manhole is competing with the other nozzles for the space on the vessel head. Orientation for manholes that are located in the tray section of the vessel is more complicated. The location of between the tray manholes has a number of restrictions. These restrictions include the type of trays and the tray spacing. The first choice for the location of a manhole is between the downcomers. The last choice is in the downcomer space, but behind the down comer. The down comer would be fitted with a removable panel to allow further access into the vessel. The location to be avoided is above a downcomer where there is the potential for falling down in the downcomer space and injury. It would be better to seek approval to move the manhole up or down one tray than placement over a downcomer.
Manhole orientation in the surge section of a vessel is not as restrictive. The surge section of a vessel is the bottom portion that, during operation will contain a large volume of liquid. Any orientation is possible for a manhole in this section. However, the location of all manholes should be in the back half of the vessel away from the pipe way. The surge section may have a large baffle plate bisecting the diameter of the vessel and extending vertically many feet. A removable plate or hatch may be installed in this baffle (by vessels) to allow access to the far side. The vessel orientation of the manhole should not hit the baffle or be located so close to the baffle that entrance is obstructed.
- Supporting Equipment:
- Flare Stacks: Locate the flare stack upwind of process units, with a minimum distance of 200 feet or 60 meters from process equipment, tanks, and cooling towers. If the stack height is less than 75 feet or 25 meters, increase this distance to a minimum of 300 feet or 90 meters. These minimum distances should be verified by Company Process Engineering.
- Furnaces: Locate fired equipment, if practical, so that flammable gases from hydrocarbon and other processing areas cannot be blown into the open flames by prevailing winds. Shell to shell horizontal clearance from hydrocarbon equipment should be 50 foot or 15 meters with the exception of reactors or equipment in alloy systems which should be located for economical piping arrangement. Provide sufficient access and clearance at fired equipment for removal of tubes, soot blowers, air pre-heater baskets, burners, fans, and other related serviceable equipment. Clearance from edge of roads to shell should be 10 foot or 3 meters. Pressure relief doors and tube access doors should be free from obstructions. Orient pressure relief doors so as not to blow into adjacent equipment. The elevation of the bottom of the heater above the high point of the finished surface, should allow free passage for operation and maintenance. In case of furnace piping, locate snuffing steam manifolds and fuel gas shut off valves at a minimum distance of 50 feet or 15 meters horizontally from the heaters they protect. Burner valves for a floor fired furnaces should be a combination of oil and gas firing valves. It should be operable from burner observation door platform. For those fired by gas only, the valves should be near the burner and should be operable from grade. Burner valve for a side fired furnaces should be so located that they can be operated while the flame is viewed from the observation door.
- Heat Exchangers: Heat exchangers come in a variety of designs. In a process facility shell and tube exchangers are the most common and are manufactured in accordance with the Tubular Exchanger Manufacturers Association code. The most common type of industrial heat exchanger is the shell and tube type where one stream, usually the one that leaves the most deposit like cooling water, flows through the tubes and the other stream goes through the shell side. This is because the tubes are easier to clean than the shell. Provision must be made to withdraw the tubes for cleaning and this area must be kept free of piping and other obstructions. Shell and tube exchangers are manufactured in accordance with the Tubular Exchanger Manufacturers Association code.
- Shell and Tube Exchangers: Shell and tube exchangers should be grouped together wherever possible. Keep channel end and shell covers clear of obstructions such as piping and structural members to allow unbolting of exchanger flanges, and removal of heads and tube bundles.
- Stacked Shell and Tube Exchangers: Stacked shell and tube exchangers should be limited to four shells high in similar service; however, the top exchanger should not exceed a centerline elevation of 18 feet or 5.5 meters above high point of finished surface, unless mounted in a structure.
- Maintenance Requirements: Exchangers with removable tube bundles should have maintenance clearance equal to the bundle length plus 5 feet or 1.5 meters measured from the tube sheet to allow for the tube bundle and the tube pulling equipment. Minimum maintenance space between flanges of exchangers or other equipment arranged in pairs should be 1 foot 6 inches or half meter. Exchanger maintenance space from a structural member or pipe should not be less than 1 foot or 300 millimeters.
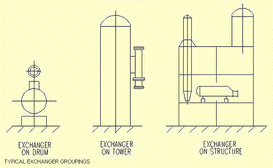
- Piping at Shell and Tube Exchangers:
- Reboilers: Locate kettle reboilers at grade and as close as possible to the vessel they serve. This type of reboiler is identifiable by its unique shape. It has one end much like a normal Shell and Tube exchanger then a very large eccentric, bottom flat transition to what looks like a normal horizontal vessel. You could also call it a Fat exchanger. The flow characteristics on the process side of a kettle reboiler are the reason for the requirement for the close relationship to the related vessel. Reboilers normally have a removable tube bundle and should have maintenance clearance equal to the bundle length plus 5 feet or 1.5 meters measured from the tube sheet.
- Double Pipe Exchangers: These exchangers can be mounted almost anywhere and with process engineer approval, they can be mounted in the vertical when required. A G-Fin Exchanger is recognizable by its shape. One segment looks like two long pieces of pipe with a 180 degree return bend at the far end. It is one finned pipe inside of another pipe with two movable supports. This type of exchanger can be joined together very simply to form multiples in series, in parallel or in a combination of series or parallel to meet the requirements of the process. This exchanger is not normally used in a service where there is a large flow rate or where high heat transfer is required. The key feature with this exchanger is the maintenance. The piping is disconnected from the tube side, which is the inner pipe. On the return bend end of this exchanger there is a removable cover. When the cover is removed this allows for the tube, or inside pipe to be pulled out. This exchanger is normally installed with the piping connections toward the pipe rack.
- Plate Heat Exchangers: A plate heat exchanger is a type of heat exchanger that uses metal plates to transfer heat between two fluids. This has a major advantage over a conventional heat exchanger in that the fluids are exposed to a much larger surface area because the fluids spread out over the plates. This facilitates the transfer of heat, and greatly increases the speed of the temperature change. Plate heat exchangers are now common and very small brazed versions are used in the hot-water sections of millions of combination boilers. The high heat transfer efficiency for such a small physical size has increased the domestic hot water flow rate of combination boilers. The small plate heat exchanger has made a great impact in domestic heating and hot-water. Larger commercial versions use gaskets between the plates, smaller version tend to be brazed. The concept behind a heat exchanger is the use of pipes or other containment vessels to heat or cool one fluid by transferring heat between it and another fluid. In most cases, the exchanger consists of a coiled pipe containing one fluid that passes through a chamber containing another fluid. The walls of the pipe are usually made of metal, or another substance with a high thermal conductivity, to facilitate the interchange, whereas the outer casing of the larger chamber is made of a plastic or coated with thermal insulation, to discourage heat from escaping from the exchanger.
- Fin Fans (Air Coolers): Air Coolers are in typically used in the cooling of the overhead vapor from tall vertical vessels or towers such as Crude Fractionators and Stripper Columns. The natural flow tends to follow gravity, where the tower overhead is the high point then down to the Air Cooler, then down to the Accumulator and finally the Overhead Product transfer pumps. With this in mind the Air Coolers are normally located above pipe ways. This conserves plot space and allows the pipe rack structure with it's foundation to do double duty with only minor up grade to the design. If the pipe rack is not used then plot space equal to the size of the Air Cooler is required. In addition a totally separate foundation and stand alone structure is required. Air coolers, or fin fans, are utilized globally in modern process facilities. Air is quickly moved past the tube exterior by way of a large fan system. As the product travels through the tubes, this process transfers the heat from the product into the atmosphere. An air cooler or fin fan unit is constructed of several hundred to several thousand externally finned tubes. Tube dimensions typically range from 1 inch or 25.4 millimeters to 1.5 inch or 38 millimeters in diameter and up to 75 feet or 23 meters in length.
|
|