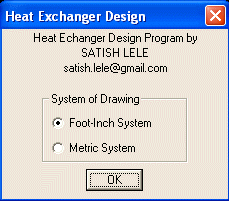 You can select the Foot-Inch units or Metric Units for the Design. All inputs will be in selected unit system. |
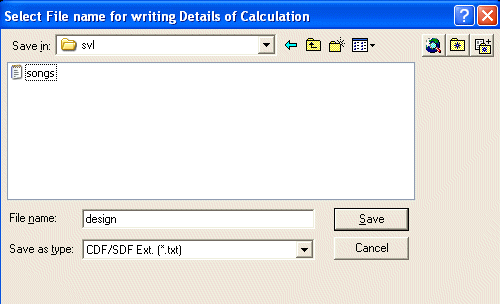 Type Name of txt file in which all process details will be written. |
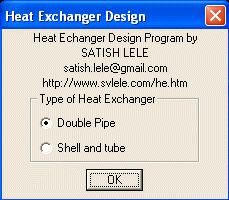 Select Double Pipe or Tubular Exchanger. |
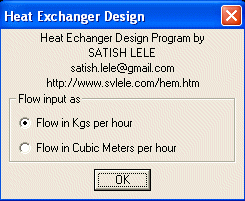 Flow in Kgs per hour or cubic meters per hour. |
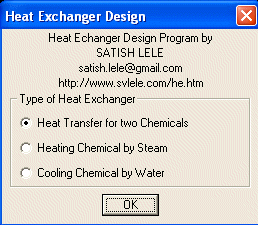 You can select type of Tubular Exchanger. |
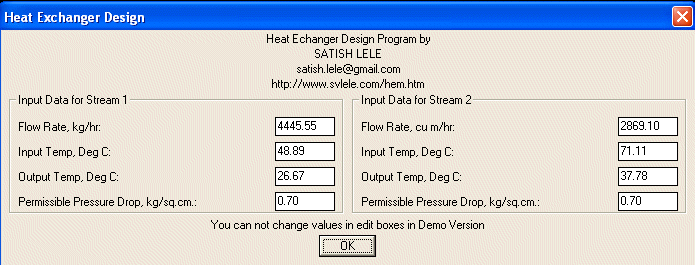 Properites of liquids in two streams. |
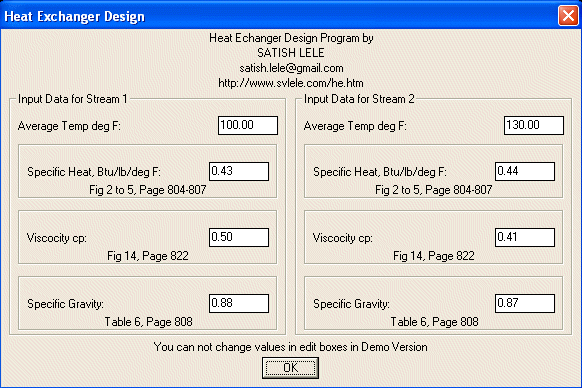 Physical Properties of two Streams. |
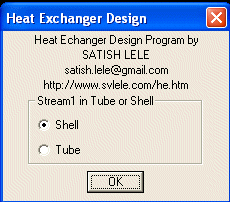 Stream one in Shell or Tube. |
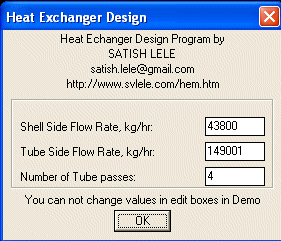 Design Program for Tubular Heat Exchanger shows flow rates on two sides. The division of Tube side flow by Shell side flow gives number of passes on tube side. |
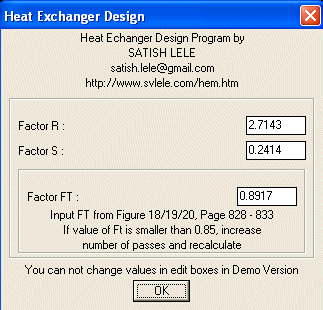 Based on number of Passes R and S factors are calculated. With these Factor FT is calculated. |
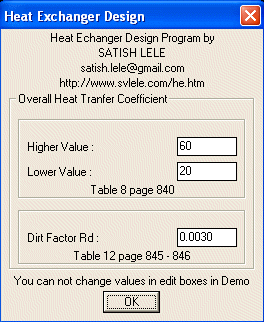 Enter Higher and Lower Values of Heat Transfer Coefficients and Dirt Factor. |
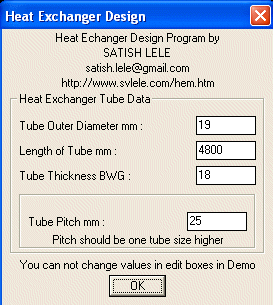 Sizes of Pipes. |
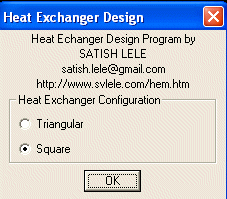 You can select either Square pitch or Triangular pitch. |
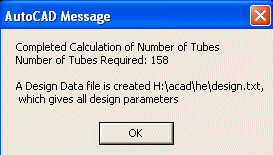 After Calculating Design Program for Tubular Heat Exchanger shows number of Tubes required. |
here to see Dialog Boxes in Imperial Units
How the Design Program for Tubular Heat Exchanger Calculates?
Design Program for Tubular Heat Exchanger first picks up flow rates, and then inlet and outlet temperatures for two streams. Out of these six values, if one is not known, Design Program for Tubular Heat Exchanger calculates values, based on other five. Design Program for Tubular Heat Exchanger also asks for permissible pressure drop on two streams. Design Program for Tubular Heat Exchanger then calculates average temperatures of two streams. Based on these average temperatures, Design Program for Tubular Heat Exchanger asks for specific heat, viscocity and specific gravity of two streams.
Stream with lower flow rate and higher temperature difference is placed Shell side. The number of passes on tube side is ratio of flow rate on tube side to flow rate on shell side, which is rounded to even number.
Design Program for Tubular Heat Exchanger then calculates LMTD. Depending on number of passes, Design Program for Tubular Heat Exchanger calculates correction factor for LMTD, and corrects LMTD by that factor. Design Program for Tubular Heat Exchanger then asks for expected Higher and Lower value of Overall Heat Transfer Coefficient and value of dirt factor. Design Program for Tubular Heat Exchanger then asks for OD, Pitch, Thickness and Length of tube. Based on these, calculation is done. Initially programs assumes number of tubes equal to number of passes. Based on this tube count, Design Program for Tubular Heat Exchanger assigns shell diameter (as per number of passes). You can select Square or Triangular Pitch for tubes.
Calculation of number of Tubes:
For Shell: Design Program for Tubular Heat Exchanger calculates Mass Velocity for shell by dividing shell side mass flow rate by shell cross sectional area. Design Program for Tubular Heat Exchanger then calculates equivalent diameter of tube. Based on this Design Program for Tubular Heat Exchanger calcuates Reynold's number. Based on Reynold's number, Design Program for Tubular Heat Exchanger picks up value of jH for shell automatically. Design Program for Tubular Heat Exchanger then calculates Overall Heat Transfer Coefficient, ho for outer side of tube.
For Tubes: Design Program for Tubular Heat Exchanger calculates Mass Velocity for tube by dividing tube side mass flow rate by cross sectional area of tube. Based on this Design Program for Tubular Heat Exchanger calcuates Reynold's number based on inner diameter of tube. Based on Reynold's number, Design Program for Tubular Heat Exchanger picks up value of jH for tube automatically. Design Program for Tubular Heat Exchanger then calculates Overall Heat Transfer Coefficient, hi for inner side of tube.
Design Program for Tubular Heat Exchanger then corrects the two values for viscocity of liquids at wall temperature. Overall Heat Transfer Coefficient is then calculated based on ho, hi and dirt factor. The heat transfer area required is calculated by dividing heat load by LMTD and value of Overall Heat Transfer Coefficient. Dividing heat transfer area by tube's outer surface area gives the number of tubes required. If calculated tubes are more than number of tubes assumed, Design Program for Tubular Heat Exchanger increases number of tubes assumed by one and recalculates. Design Program for Tubular Heat Exchanger follows this procedure till number of assumed tubes are same as number of calculated tubes.
Calculation Pressure Drop:
For Tube: Based on Reynold's number calculated earlier, Design Program for Tubular Heat Exchanger picks up value of friction factor and calculates pressure drop.
For Shell: Based on Reynold's number calculated earlier, Design Program for Tubular Heat Exchanger picks up value of friction factor. Based on number of passes (due to baffles), Design Program for Tubular Heat Exchanger calculates pressure drop due to friction. If the shell side pressure drop is not within limit, Design Program for Tubular Heat Exchanger increases gap in baffle, till pressure drop is within limit.
If the pressure drops on both sides is within limit, design is good. Otherwise new combination of OD, Pitch, Thickness and Length of tube is tried to get the result.
Report Generated by Design Program for Tubular Heat Exchanger
==============================================================
*Process Design
Units of Calculation : Imperial
Input Values in Metric system
==============================================================
Type : Shell and Tube Heat Exchanger
==============================================================
Duty : Inter Changer for two Chemicals
==============================================================
*Input Parameters
Shell side flow rate : 19510.00 kg/h
Shell side inlet Temp : 198.89 Deg C
Shell side outlet Temp : 93.33 Deg C
Shell side Allowable Pressure Drop : 0.35 Kg/sq.cm.
Shell side liquid Specific Heat : 0.6128 Btu/lb-Deg F
Shell side liquid Viscosity : 0.40 cP
Shell side Specific Gravity : 0.7300
Tube side flow rate : 67605.00 kg/h
Tube side inlet Temp : 76.67 Deg C
Tube side outlet Temp : 37.78 Deg C
Tube side Allowable Pressure Drop : 0.70 Kg/sq.cm.
Tube side liquid Specific Heat : 0.4890 Btu/lb-Deg F
Tube side liquid Viscosity : 3.60 cP
Tube side Specific Gravity : 0.8300
==============================================================
Stream 1 on Shell side
Number of Tube Side Passes : 4
Factor R : 2.7143
Factor S : 0.2414
Factor Ft : 0.8917
Corrected LMTD : 135.71
Dirt Factor Rd : 0.0030
Heat Transfer Load : 5100320.06 Btu/hr
==============================================================
*Tube Data
Tube Outer Diameter : 25 mm
Length of Tube : 4800 mm
Tube Thickness BWG : 13
Tube Pitch : 32 mm
Tube Configration : Square
==============================================================
*All Calculations done in Imperial Units
Tube Side Flow Area : 0.1404 sq. ft.
Tube Side Mass Velocity : 1061465.81 ft/h
Tube Side Reynold's Number : 8224
Tube Side jH value : 30.2000
Tube Side mean Temp : 129.40 Deg F
Tube side c Value : 0.4900
Tube side k Value : 0.0770
Tube side Heat Transfer Coefficient h : 106 Btu/h-sq. ft. Deg F
Tube side Heat Transfer Coefficient h (corrected for viscocity) : 120 Btu/h-sq. ft. Deg F
Shell Side Flow Area : 0.1442 sq. ft.
Shell Side Mass Velocity : 298095.66 ft/h
Shell Side Reynold's Number : 25662
Shell Side jH value : 92.0000
Shell Side mean Temp : 279.80 Deg F
Factor Fc : 0.42
Shell side c Value : 0.59
Shell side k Value : 0.08
Shell side Heat Transfer Coefficient h : 165.06 Btu/h-sq. ft. Deg F
Shell side Heat Transfer Coefficient h (corrected for viscocity) : 157.47 Btu/h-sq. ft. Deg F
==============================================================
*Pressure Drop in Imperial Units
Shell side Pressure Drop
Shell Side Reynold's Number : 25662
Shell side passes : 40
Gap in Baffles : 4 7/8"
Shell side Friction Factor : 0.0018
Shell side Mass Velocity : 298095.66 ft/h
Shell ID : 1'-9 1/4"
Shell Liquid specific gravity : 0.7300
Equivalent Dia of Tube : 1
Shell side Pressure Drop : 0.2608 kg/sq cm
--------------------------------------------------------------
Tube side Pressure Drop
Tube Side Reynold's Number : 8224
Tube side passes : 4
Tube side Friction Factor : 0.0003
Tube Liquid specific gravity : 0.8300
Tube Side Mass Velocity : 1061465.81 ft/h
Length of Tube : 4800 mm
Inside Dia of Tube : 1
Tube side Friction Loss : 0.4523 kg/sq cm
Velocity Head : 0.1700 psi
Tube side Velocity Loss : 0.2302 kg/sq cm
Tube side Pressure Drop : 0.6827 kg/sq cm
==============================================================
Summary:
Number of Tubes : 158
Shell side passes : 40
Number of Baffles : 39
Recommended Shell NB : 550 mm
Gap in Baffles : 124 mm
==============================================================
|