When hot fluid passes through a pipe line, the pipe line expands along its length. When the fluid stops flowing or if line is emptied, it cools and contracts to original length. If the pipe is running on grade or pipe rack, it is generally quite long and it may increase in length by 50 mm. To compensate for the change in length, expansion loops are provided. The expansion loops absorb the increase in length by deflecting. These are of different types. The loop can be in one direction. The direction is decided on the basis of availability of space.
U Bends
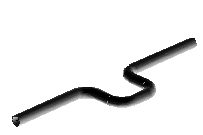
The following form loop in two directions. The top center point of loop rests on structure.
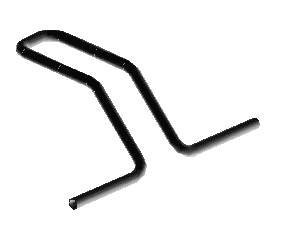
The pipe line is anchored between the two loops. The hot line generally has a shoe, which is welded to the structure, so that pipe line at that point can not move in any direction. The structure at that point is made of columns and cross bracings. This does not allow any movement of structure and pipe. Guide supports are provided along the length of pipe, so that pipe line expands only in one direction.
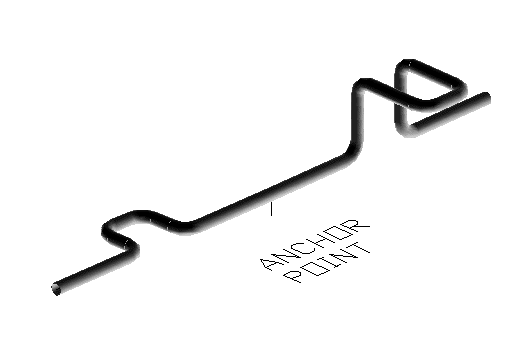
For lines inside plant, the direction of the line is changed every 4 to 6 meters. This allows the pipe line to expand at the end of pipe line. Sufficient gap is provided for the pipe to expand.
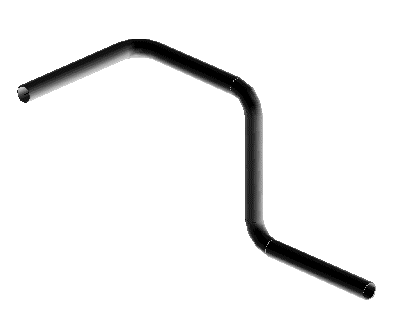
The pipe routing for the stresses can be analyzed using some software like CAESER II, and others.
Properties of pipes and fittings are entered for the program to calculate stresses. Some of these are
- Diameter of the pipe
- Thickness of the pipe
- Temperature of material flowing through the pipe
- Material of Construction of the pipe
- Weights of fittings like elbows, tees, valves etc.
The profile of pipe line is created in 3D and then checked for stresses in each pipe. The stresses are maximum at critical points, like welds. The stresses are due to smaller length of adjoining pipe. If a line is found stressed, the line length is adjusted to remove stress.
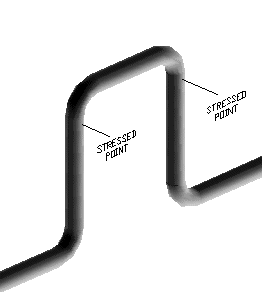
If stress is not reduced, some loop are put in lines. Some anchoring points are added or moved to reduce stress.
Understanding of material classification systems, material specifications, and material properties is often limited to a few grades of carbon steel or to a specific alloy system employed by the user on a regular basis. B31.3 is a safety code focusing primarily on mechanical design, mechanical properties, and resulting pressure integrity.
Material Classification Systems and Specifications: Three primary methods of identifying materials are:
a) generic designations
b) trade names or proprietary designations
c) standardized alphanumeric designations
These material designation systems are discussed in more detail in the table.

FABRICATION, ASSEMBLY, AND ERECTION
Chapter V of the B31.3 Code is devoted to the fabrication, assembly, and erection of piping systems. These terms are defined as follows.
- Fabrication is the preparation of piping for assembly, including cutting, threading, grooving, forming, bending, and joining of components into subassemblies. Fabrication may be performed in the shop or in the field.
- Assembly is the joining together of two or more piping components by bolting, welding, bonding, screwing, brazing, soldering, cementing, or use of packing devices as specified by the engineering design.
- Erection is the complete installation of a piping system in the locations and on the supports designated by the engineering design, including any field assembly, fabrication, examination, inspection, and testing of the system as required by the Code.
Fabrication, assembly, and erection require the use of many special processes including:
- forming and bending by cold and hot methods
- joining by welding, brazing, soldering, or mechanical methods including threading, flanging, specialty high pressure connections, and mechanical interference fits (MIF)
- heat treatment by local methods, or by permanent or temporary furnaces
Bending: The need for changes to the direction of flow in piping systems has traditionally been accommodated through the use of manufactured fittings such as elbows and tees. However, changes to direction of flow may also be made through the use of pipe bends. Bends are usually referred to in terms of:
- method of manufacture, including cold bends, hot bends, furnace bends, induction bends, arm bends, ram bends, three point bends, miter bends, segmented bends, corrugated bends, and creased bends
- location of manufacture, that is, field bends or factory bends
- shape or appearance, such as L-bends, S-bends, wrinkle bends, miter bends,
segmented bends, corrugated bends, and creased bends
- function or end use, such as sag bends, over bends, side bends, and combination bends