
 Pongamia Pinnata
BioFuels
Neem
Mahua
Castor
Undi
Kokam
Fish Oil
Fatty Oils
Expellers
BioGas
Organic Fertilizer
 Jatropha
 BioDiesel
 Consultancy
Algae
Herbal Product
 Climate Adaptation
Contact Me
My Resume
|
 BIO-GAS PLANT
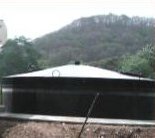
Disposal of Cow Dung is one of the major problems being faced by Producers of Dairy Product across the world. Cow Dung is not a problem but Cow Dung is a big asset. There are two ways of processing these to produce Organic Fertilizer.
Bio Gas Plant : Here the Biomass is digested in a simple plant and Bio Gas produced is stored and used. The area required for plant is very small.
Composting : Here the Biomass is digested underground but Bio Gas is not produced and fuel potential is wasted. Composting needs large area of land.
A Dairy plant, produces 2.5 to 3 tons of Cow Dung. If we carefully analyze this waste, we will realize that majority of waste is biodegradable. Cow Dung can be converted to valuable organic fertilizer. Generally a slurry of 8 to 10% solids is used in Bio Gas plant, and one can get 350 Kilo Calories per Kg of Cow Dung cake.
When compared with other organic sources, (manures, oil seed cakes), Cow Dung provides essential nutrients at comparable levels. This biodegradable waste, if handled properly would maintain the natural balance of essential elements and thereby promote more harvests from nature.
Disposal of Cow Dung, can be achieved by several other means like incineration, landfills, dumping in the sea or other water bodies etc. These methods have their own hazards. Incineration can lead to respiratory illnesses. Moreover, incineration may lead to disruption of biogeochemical cycles of several elements and will have long term effects on biosphere. Landfill and dumping can pollute water bodies.
Bio Gas Plant would serve many purposes such as:
Environment friendly disposal of waste, which is need of hour considering mass pollution everywhere.
Generation of fairly good amount of fuel gas, which will definitely support the dwindling energy resources.
Generation of high quality manure, which is an excellent soil conditioner. This is very important for replenishing fast decreasing resources of productive soils. It must be noted that need for replenishing the soil with high quality organic manure has been identified in plan documents.
Biogas is a colour less, odour less and flammable gas. The gas generated in this plant can also be used as a source of natural gas. The production of biogas, is about 0.25 to 0.35 cubic meters per kg of cake fermented, with following composition of biogas
Amount of Bio Material required for production of 1 cubic meter of BioGas (equivalent to 400 gms of LPG, fuel for 3 to 4 people).
Stale, left over food: 5 kgs
Animal Dung: 25 kgs
Chicken dung 2 kgs + animal dung 10 kgs
Spoiled flour of wheat / corn: 1.5 kgs
Production Plant of Bio-Gas
According to the United Nations' Food and Agricultural Organization (FAO), there are about 1.3 billion cattle worldwide (one for every five people), slightly more than 1 billion sheep, around 1 billion pigs, 800 million goats and 17 billion chickens. Between them, they produce a lot of fecal matter, around 13 billion tons per year, according to various estimates.
That matter contains 55% to 65% of methane, which when released into the atmosphere is bad news for us (Methane traps heat at 23 times the rate that carbon dioxide does) but when burned is another matter entirely. BioGas gives us energy.
62.5 liters of bio gas can be produced from one kilogram (one cubic foot of bio gas can be produced from one pound) of cow manure (heated at around 28oC, or 82.4oF). That is enough to cook one day's worth of meals for four to six people in India. One cow in one year can produce enough manure, which when converted into methane can match the fuel provided by 200+ liters (about 53 U.S. gallons) of gasoline. Around 7,500 cattle can produce gas equivalent to 1 megawatt (MW) of electricity. Oil seed cakes can very well substitute cow dung, once bio gas plant is stabilized using cow dung as seed material.
Bio Gas Plant : Biomass is digested in a simple plant and Bio Gas produced is stored and used. The area required for plant is very small. A paste of cake in water, is generally fed to digester. Solids concentration should be around 8 to 10%. Bio Gas is formed within 1 to 5 days.
Operation
The material to be processed is brought to the plant site every day. Two workers are needed for the operation of the plant. The important tasks to be done are:
Transport of waste materials
Processing the waste in mixer
Routine operations for pre-digester and digester tanks
Manure pits
Infrastructure Required
Infrastructure required to set up a Bio gas plant of a capacity of 1 ton /day of Cow Dung Cake is as follows:
Area of Plot: 300 m2
Manpower: Two unskilled persons
Power supply: 1 KW
Water Supply: 1,200 liters
Cost: Indian Rupees 5,00,000
Construction of a Bio-gas Plant
Criteria for Bio-gas Plant
BioGas plant owner who wants to build a bio-gas plant must have Cow Dung cake to sustain the operation of the plant. The minimum amount of cake should be 3 to 4 tons per day.
Cake storage enclosure should not be more than 20 meters from the bio-gas construction area.
There must be drainage alley from cake storage area, connected directly to the bio-gas plant.
Access to ground water round the year and the water source should not be farther than 20 meters from the bio-gas plant.
Bio gas usage should not be placed further than 100 meters form the plant.
The owner must have interests in using gas, fermented manure and want to build a bio-gas plant to reduce the pollution in environment.
Required budget, materials and labour to build bio-gas plant.
Time and labour in maintenance of bio-gas plant.
Design of Bio-gas Plant
The fixed dome of bio-gas plant is buried underground. There are 3 main connecting parts:
Feed Section where Cow Dung cake is mixed with water before Cow Dung cake is poured into digester chamber.
Digester Section where Cow Dung cake is fermented in 3 sections (Primary, Secondary and Tertiary Decomposer). Methane and other gases will be produced in the chamber and these gases will push manure and slurry at bottom of the floor into expansion chamber.
Exhaust Section which collects excess manure and slurry. When gas is being used, manure and slurry will flow back into digester chamber to push gas up for usage. When the excess manure exceeds the volume of the chamber, the manure will be drained out.
This system is called dynamic system, when gas is produced inside the pit, the gas pressure will push manure and slurry at the bottom of the pit to flow up into expansion chamber. When this gas is used, the slurry in the expansion chamber will flow back into the digester chamber to push the gas up for usage. This happens consistently. The plant will be operated efficiently for a long period of time if the gas pit does not get cracked and the system runs regularly. In each case the strength of the plant depends on fine construction, specification of materials, and strict adherence to the maintenance of the bio-gas plant.
Location of the Bio-gas Plant
The plant should not be located farther than 5 meters from the Cow Dung cake enclosure. The digester chamber must be in an open area and should not be near any water source or natural water, as water coming out from Bio Gas plant may seep into underground water. The plant should also be situated on a slope and not on the low land to avoid the danger of floods. The excess manure from expansion chamber should flow into the open pit or the storage tank and not into natural water bodies such as rivers to avoid the risk of pollution. The bio gas plant must have a concrete slab floor enclosure with a drainage alley, with 1% gradient. If the floor is not on slope, floor must be elevated. For larger plants, a continuous rotary vacuum filter can be installed to filter out water from cake, for reuse.
Construction of Bio Gas Plant
Locate the lowest point of drainage alley and mark 30 cm above this point. Mark a peg on the opposite side and balance the level between the peg and the mark over the alley with level adjusting hose. From the mark on the level line, set the center of digester chamber on the ground surface by using plumb. Draw the line to mark the size of digester chamber.
To locate the storage tank, measure from the center of digester chamber. Find the lowest point to set the outlet point which is 60 cm lower than the level line and at least 15 cm over the ground to prevent the outside water to flow into the chamber. If the lowest point can not be located, check the drainage alley for the possibility of being elevated or excavated. When the outlet point is found, the temporary level line becomes level line. Cross another permanent level line to the first line at the center of the digester chamber to locate the center of digester chamber. The location of expansion chamber should be on the opposite side of the mixing chamber or not over 45o.
Think before excavating: Ensure that the diameter of the pit excavated, is consistent with diameters at the top and the base, and at depth below level line. Place excavated soil 50 cm away from the edge of the pit and do not put BioGas plant on the ground where the expansion chamber, mixing chamber or outlet pipe will be constructed. It is a waste of time, to remove this pile of soil later. Do not excavate deeper as the base of the chamber may not be strong enough. If there is any seepage, a small trap pit must be dug next to the outer edge of digester chamber base. The floor of the trap pit should be lower than the digester chamber so that ground water can flow into the trap pit. When the required final depth is obtained, set the center at the base of digester chamber by crossing the level line and use a plumb to locate the center of the digester chamber. Excavate soil in the outer circle to a depth of 25 cm and draw another circle. Excavate soil in the inner circle to a depth of 5 cm.

Elevation and Plan

Sectional Views
Design Data and Detailed Fabrication Drawings of this type are available based on Cow Dung available, for US$ 15 or 1,000 each. Kgs of dry Cow Dung available per day
- 100
- 250
- 500
- 1,000
- 2,000
- 3,000
- 5,000
- 10,000
- 20,000
- 30,000
| |
You can send payment through
You can buy Drawing Package by sending money by PayTM. Send payment to cell no. 91-9403405715.
OR
Telegraphic (Wire) Transfer to my bank account in , the details of which are as follows:
Name of Account : SATISH LELE
Account No. 05401000053720
Swift Code : HDFCINBB
IFSC Code : HDFC0000540
MICR Code : 400240002 061159 10
Account type : Savings Account
Name of Bank : HDFC Bank, Vashi Branch,
Address : HDFC Annex, Plot 82, Sector 17, Vashi, New Bombay, 400703. India.
Tel : 91-22-27892969.
Fax : 91-22-27892957.
The Drawings will be sent to you immediately by eMail. |
|