
 Pongamia Pinnata
BioFuels
Neem
Rice Bran
Mahua
Castor
Undi
Kokam
Fish Oil
Fatty Oils
 Expellers
BioGas
Organic Fertilizer
 Jatropha
 BioDiesel
 Consultancy
Algae
Herbal Product
 Climate Adaptation
Contact Me
My Resume
|
Indian Oil Expeller Manufacturers
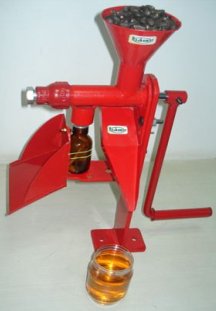 Hand Operated Expeller
Tinytech Plants, Tagore Road, Rajkot, 360 002, India, Tel: 91-281-248 0166, Fax: 91-281-246 7552, Mr. Gopal Desai, M: 91-92276 06264. www.tinytechindia.com. tinytech@tinytechindia.com.
Troika Group of companies, Embassy Centre, Nariman Point, Mumbai, 400 021, India, Tel: 91-22-2283 4429, 2283 4334. Fax: 91-22-2282 3778, troika@vsnl.com, www.troikaindia.com.
Jagdish Exports, Gondal Road, Rajkot, 360002, India, Tel: 91-281-2461134 / 2462079 / 2463055 / 2451214, Fax: 91-281-2461770 / 2450628, info@jagdishexports.com. Web: www.jagdishexports.com
Gagan International, Nirankari Street No. 3, G.T, Road, Miller Ganj, Ludhiana, 141 003, India, Tel: 91-161-2532134, 2531589, 2535814. Fax: 91-161-2543442, Mr. Gagan Goyal, M: 91-98147 22255. sales@oilmillspares.com.
Nitya Engineers, Nirankari street no. 3, G.T. Road, Miller Ganj, Ludhiana, 141 003, India, Tel: 91-161-2541575, 91-161-2501911, Mr. Sushil Singla, M: 91-98150 22911. nityaenterprise@yahoo.com, www.oilextractmachinery.com
Rajkumar Agro Engineers Pvt. Ltd., Near Union Bank, Ghat Road, Nagpur, 440 018, India. Tel : 91-712-2725271, 91-712-2772570, Mobile : 91-9422807682, www.rajkumarexpeller.com, rajkumarexpeller@gmail.com
Amrut Engineering Works, Shakti Compound, Near Jain Temple, behind Vihar Theater, Pratap Nagar, Vadodara, 390 004, India. Tel: 91-265-3229762, 2439348, Fax: 91-265-2438865, Mr. Kartikrao Chavan, M: 91-93272 29762.
Chetan Agro Industries, 11 Bhaktinagar station plot, Rajkot, 360 002, Gujrat, India, Tel: 91-281-2461781, Fax: 91-281-2461782.
Kumar Metal Industries Pvt. Ltd. 101, Kakad Bhavan, 30th Road, opp. Gaiety Galaxy Cinema, Bandra (West), Mumbai, 400 050, India. Tel : 91-22-2644 1673/1674, Fax: 91–22-2642 8136, www.kumarmetal.com, info@kumarmetal.com
Arian Engineering Pvt. Ltd., 224, Akansha, Plot 2, Press Complex, Zone 1, M P Nagar, Bhopal, 462016, India, Tel: 91-755-4274796, Fax: 91-755-2578835, Mr. Hemant K Tata, Director, M: 91-98260 27472, www.arianengg.com, arianengg@gmail.com.
Vegetable Oil Expellers
Extraction of Oil: Oil can be expelled from seeds in normal screw type Oil Expeller. The expeller is quite simple and quite inexpensive. Oil Expeller crushes seeds along with its cover. The oil is then immediately filtered through a filter press and used for the manufacture of BioDiesel. Oil cake is sent to Bio-Gas plant.
Tiny Oil Expeller Mill of 5 tons per day capacity
Most Mills are suitable for crushing all types of oilseeds whether edible or non edible. Filtration of oil is done, giving transparent pure natural and convincing appearance to the oil. Decorticator has special provision for shelling the seeds without breakage. In case of Jatropha seeds, decorticator is required, as shellof 80% of the seed is removed and only about 20% of seed is crushed with shell. These 20% shells give roughness to cake when crushed and cake is pushed out easily. Yield of oil is high, because of highly scientific worm sequence inside the chamber cage. Maintenance expenses are negligible. Diesel consumption in engine is only 1.25 liter per hour. Technology is so simple that person can be trained only in 3 days to operate the mill. Video cassette or CD is provided, by some parties, with every export mill to explain operation, maintenance, names of components, dismantling, assembling etc.
% Oil Extraction of Different Oil Seeds: Typical oil extraction in kilograms, from 100 kilograms of best quality oil seeds will be as under
Palm Kernel | 36 | Soy bean | 14 |
Sesame | 50 | Palm Fruit | 20 |
Rape seed | 37 | Groundnut Kernel | 42 |
Mustard | 35 | Castor Seed | 36 |
Lin seed | 42 | Sunflower | 32 |
Cotton Seed | 13 | Coconut | 13 |
Jatropha | 25 | Karanj | 24 |
Special Facilities in Tiny Expeller: Chamber cage opens on hinges simply by tilting of chamber halves. Drudgery weights of clamping bars and chamber halves, is totally eliminated. Thickness of cake can be changed while running of expeller. This is unique facility which enables to find and adjust cones at the optimum point. Oil pump is integral part of the expeller and hence no separate pump is required. Due to ready foundation frame, no concrete foundation is required in the ground. So you can start the mill in 24 hours. Also you can shift the machine from one place to another as and when required. 6 taper roller bearings make expeller very sturdy and durable. No ball bearing fitted any where. As expeller is very compact. Oil Expeller is economical to transport.
Basic Requirements:
Shed: About 300 sq. ft. 15' X 20' (5 meters X 6 meters)
Manpower: Only two persons, one skilled and other unskilled.
Capital: Cost of Expeller + working capital.
Power: Expeller is run by 10 H.P. Electric Motor or by a 12 H.P. oil engine (if electrical power is not available).
Highly experienced mill operator can extract oil without cooking from some oilseeds such as rape seeds, cottonseed, sesame, sunflower, jatropha, karanj etc. For Groundnut, Palm kernel, Castor seed, cooking is essential. Refining of oil is not required. Filtered oil is best for use. Filtered Jatropha oil has a minimum shelf life of 1 month. However, cottonseed oil requires refining or at least neutralizing. Castor seed oil requires steam heating in a neutralizer vessel before filtration. For palm fruits, conventional expeller will not be useful. Special kind of expeller with a different design is used for palm fruits and normal Oil Expeller is not useful for Palm.
Special Machinery for Oil Seeds: Decorticator shells the nut into husks and kernels. Husks are thrown away by built in air blower and kernels are screened to separate split kernels from whole kernels. Oil Expeller is run by a 2 H.P. Motor. 100 kilograms of groundnut gives about 73 kgs of kernels and 27 kgs of husks. Sunflower cracker breaks the sunflower seeds and gives the mixture of kernels and husks for crushing. Palm nut cracker breaks the palm nuts and gives the palm kernels and husks. Coconut cutter breaks the coconut cups into small pieces suitable for crushing into expeller. Oil Expeller runs by a 5 H.P. Motor. Cooking kettle heats and cooks the kernels or oilseeds. An outer steam jacket or electrical heater does the cooking. A little amount of steam or water is also added to the oilseeds to increase moisture content to optimum level. Kettle is mounted on the expeller. Its agitator is driven by power from expeller shaft. Expeller crushes oilseeds producing oil and oil cake. Filter press filters the oil. Filtered oil is a pure and fresh natural oil. Boiler provides process steam to the cooking kettle. Husks are used as fuel in the boiler. Any agricultural waste or wood can be used. Water feed pump is mounted on the boiler itself. Boiler is not required for Jatropha or Karanj seeds. (Neutralizer is required for cottonseed oil to remove free fatty acids by adding caustic soda. Neutralizer is driven by 1 H.P. Motor.) Castor oil can also be heated in neutralizer by steam coils inside the neutralizer.
Socio Economic Benefits: Tiny Oil Mills greatly encourage rural development, as wealth and self-employment jobs are generated in villages. Tiny Oil Mills save transport expenses for carrying oilseeds to cities and bringing oil from cities. Consumer’s empty tins can be refilled and hence costly packing expenses can be saved. Tiny Oil Mills make pure, fresh natural oil available to villagers from their own oilseeds on custom milling basis. So villagers are saved from profiteering, adulteration, etc. Speculation in oil and oilseed becomes impossible, due to decentralized production in Tiny Oil Mills. Tiny Oil Mills eliminate exploitation by middlemen and traders, as consumers have direct contact with mills. Tiny Oil Mills encourage animal husbandry by making oil cake available as best cattle feed, which increases production of milk considerably. Tiny Oil Mills create confidence and enthusiasm among villagers and their youngsters to run and manage rural industries. This is the greatest benefit as oil expeller accelerates creative Entrepreneurship for other industries also.
Clarification of Expeller Oil: The oil leaving expellers in oil milling plant, contains a high proportion of fine foots that are conventionally removed by passing oil through a filter press. Continuous Super-D-Canters give good results as shown below:
Capacity: 3000 SDC = 2,500 kg/hr (>50 TPD) and 3400 SDC = 5,000 kg/hr (>100 TPD). Foots Removal : 96% (without water addition) and 99% (with water addition)
The Continuous Acid / Water Degumming Process: Gums in vegetable oil need to be removed to avoid reversion of color and taste, during subsequent refining steps. The process involves a single stage phosphoric acid treatment and a single stage hot water treatment, followed by continuous removal of the hydrated gums in a Degumming Super Centrifuge.
Advantages: Availability of cleaner oil down stream, reduced oil loss in the caustic refining step, and thus higher yield of refined oil can be obtained. Gums obtained have a ready market. Soap stock obtained during caustic refining can be directly used for soap making. Removal of gum reduces the requirement of catalyst and consequently reduces the oil loss during hydrogenation.
Applications: The continuous acid water degumming process can be used to refine the following oils: Groundnut Oil, Cottonseed oil, Rice Bran Oil, Palm Oil, Mustard Oil, Corn Oil, Safflower Oil etc. Normal capacities of Super Centrifuge are 1 Ton / hour and 0.55 Ton / hour.
Continuous Neutralization Plant: All crude vegetable oils destined for human consumption are neutralized to remove free fatty acids, albuminous and mucilaginous matter, and thereafter washed to reduce the soap content of neutral oil to produce a more stable product. Effective neutralization results in enhanced effectiveness of subsequent steps such as bleaching, hydrogenation, winterizing, deodorizing and furthermore results in high yields of a quality product. Neutralization also results in removal of phosphatides, removal of free fatty acids and removal of color bodies. Removal of traces of soap and moisture occurs in the washing and drying steps.
The neutralization process consists of caustic refining and re-refining (wherever required), first water washing, second water washing and vacuum drying.
In the refining and washing steps, the separation of neutral oil from soap stock and neutral oil from wash water, is carried out in one or more high gravity super centrifuges.
Advantages: Low neutral oil loss with the soap stock, due to continuous separation in the super centrifuge operating at a centrifugal force of 13,200 or 16,000 gravities.
Control and optimization of reaction time followed by immediate centrifugal separation of soap stock minimizes oil loss due to saponification. Second stage refining enables efficient decolorization with minimum oil loss in many oils such as cotton seed oil which require heavy caustic treatment.
Plants are continuous and virtually automatic leading to ease of operation with unskilled labor which can be easily taught. Parallel bank of centrifuges at each stage of the process provides flexibility and reduces the vulnerability to mechanical failure.
Easy bowl cleaning of centrifuges, low maintenance, minimum floor space, all go to increasing refining profits. Only coconut and castor oils saponify readily. Hence the neutralization losses have to be maintained within specified limits.
Performance Figures:
| % FFA | PPM Soap | % Moisture |
After refining | 0.5 - 0.8 | 1000 – 2000 | 0.5 |
After Re-refining | <0.1 | 200 – 600 | 0.5 |
After 1st soft water washing | <0.1 | 100 | 0.5 |
After 2nd soft water washing | <0.1 | <50 | <0.5 |
After Vacuum drying | <0.1 | <50 | <0.1 |
Capacities: Plants are designed, installed and commissioned on a turnkey basis for the following capacities:
Each AS26 Super Centrifuge, Feed = 1.0 Ton / hour.
Each AS16 Super Centrifuge, Feed = 0.55 Ton / hour.
Continuous Bleaching Process: The neutral, washed and dried Vegetable Oil still contains some color bodies and small traces of soap (<50 parts per million) which have to be removed. The Continuous Bleaching Plant equipped with hermetic leaf filters, operates under vacuum to prevent oil oxidation. The oil is cold mixed with metered quantities of bleaching earth and / or other bleaching agents and thereafter heated to the correct temperature and pumped to the Continuous Bleacher operating under vacuum where an adequate retention time is provided to ensure effective bleaching. The oil earth slurry is further pumped to two hermetic leaf filters operating sequentially resulting in continuous bleached oil (filtrate) discharge.
Advantages: Continuous Bleaching Process cuts costs on labor, maintenance, spares and bleaching earth. Continuous Bleaching Process proportions bleaching earth to oil or fat, continuously and accurately. Optimum conditions of vacuum, temperature and dryness of both components, facilitate efficient deaeration and degassification of the oil-earth mixture. Continuous Bleaching Process minimizes operator attendance by fully automating the process.
Capacity: Continuous Bleaching plants are available for plant capacities of 50 TPD and above. For capacities below 50 TPD, batch bleaching process is recommended.
Deodorization: The deodorization process is highly specialized type of steam distillation under high vacuum based upon the principle of falling film to remove objectionable volatile components such a ketones, aldehydes and alcohols. The bleached oil is pumped by the feed pump to the deaerator, where the pretreated oil is degassed. This deaerated oil is passed through a heat exchanger, where the oil is heated by exchanging the heat of the deodorized oil. The oil is further heated to the stripping temperature in the preheater, wherein thermic fluid is circulated. The above mentioned oil is fed to a flash chamber and flows thereafter to an oil distributor inside falling film deodorizer. The oil descends counter current to the stripping steam in the form of very thin film and gets completely deodorized. The fatty acids distilled are condensed, cooled and stored.
The oil from the bottom, flows to an intermediate vessel having an arrangement for dosing citric acid. This deodorized oil is then pumped through a heat exchanger to the polishing filter. The filtered oil is thereafter passed through a cooler and discharged for collection.
Advantages of Falling Film Technology: Falling Film has a short hold up time during deodorization, compared to any conventional deodorizing plant. The hold up time is approximately 30 seconds, compared to 90 to 130 minutes. Deodorization takes place inside the tubes from a thin film of less than 0.3 mm thick. Thus there is a good heat as well as mass transfer, without any significant pressure drop. This plant can process heat sensitive oils without interchange effects of ester. Due to short hold up time at high temperature and under high vacuum, there is no color fixation of oils. Due to low pressure drop, the stripping steam consumption, is approximately 110 kilograms / ton of oil, which is much lower than that of conventional plants giving approximately saving on steam of 30 to 40%.
The energy consumption of the vacuum plant is essentially reduced, because a lower amount of stripping vapor has to be sucked off. The counter flow configuration of the falling film deodorizer results in lower entraining loss of oil. There is a lower water demand in the vacuum equipment due to size reduction. Fuel oil consumption is less as compared to conventional Continuous Deodorizer.
Fat Splitting: In fat splitting or hydrolysis, vegetable oils or animal fats are split into fatty acid and glycerine, merely by addition of water. The one tower fat splitting process, employs highly innovative and advanced technology for continuous fat splitting without a catalyst. The splitting takes place at a high (55 Bar) pressure in presence of water. The fat and water flow in opposite directions, resulting in high glycerin to water concentration and low steam consumption. The one tower splitting plant is totally continuous, and designed in such a way that the fat is pumped in and the fatty acid and water with glycerine is pumped out continuously. The plant is totally automated and its operation is as simple as switch button. All control instrumentation is connected to the switch board, making fat splitting possible for just one operator to supervise the splitting plant.
Advantages: Fat splitting has a minimum steam consumption (approx. 200 kilograms / ton of fat) achieved by the heat exchange in the splitting tower.
High glycerine to water concentration (with a free fatty acid content of 5% in the crude fat, the glycerine to water concentration is approximately 20%) is made possible by the specially designed water distribution system inside the top of the tower. Discharge temperature of fatty acids from the plant is at approx. 80oC.
Distillation Process of Fatty Acids: Distillation of heat sensitive fatty acids is a highly complex and difficult operation, requiring specialized process and equipment. Fatty acid distillation process is the most efficient, state-of-the-art process available in the world today, for the distillation of fatty acids obtained from high pressure splitting. Distillation is specially designed to obtain premium quality fatty acids, free from odors and low molecular weight components and minimum color contaminants, with the help of a pre-run column. The process involves stripping the maximum amount of unwanted volatiles from the fatty acids.
Equipment: The Plant consists of a de-gassing and de-watering stage, complete with a condenser /gas cooler and a condensate receiver, two pumps, a pre-run column with falling film evaporator, a product preheater, one reflux condenser, two other condensers, the main distillation column with a falling film evaporator and a residue stage falling film evaporator, a condenser serving as a product preheater for the de-gassing and de-watering stage, a final condenser, a gas cooler, a residue cooler, a distillate receiver and three pumps.
Process Description: The carriers of color and odor of split crude fatty acids (secondary components, mainly created by oxidation and decomposition with a much lower boiling point), are drawn off together with the fatty acids in the de-gassing / de-watering stage, mainly with the stripping steam added at the bottom. The fatty acids are then continuously fed to the pre-run column, where most of the remaining secondary components, the odor and color, are removed by steam distillation. The deodorization of fatty acids, and the separation of odor and color components is effected by the addition of steam to the bottom.
The fatty acids from the bottom, are pumped back partially to the column through a falling film evaporator, where the temperature is raised above 200oC by heating oil, using thermic fluid heating. The reflux is brought about by the reflux condenser. The control is effected via circulation of water. The material with odor and color, moves to the next condenser due to initial cooling by the reflux condenser. The vapors entering the next two condensers help obtain maximum recovery from the first running, separated in the liquid phase separation tank.
The fatty acids from the pre-run column, are fed into the distiller column. The acids from the bottom of this column are then pushed back partially through the column via the falling film evaporator, where the appropriate temperature to achieve the maximum rate of evaporation inside the distiller column is maintained. The distilled fatty acid vapors leaving the column transfer heat partially to the crude fatty acid in a condenser and then enter the next condenser, where the maximum recovery of the distilled fatty acids is effected. These are then collected in the distillate receiver. The necessary reduction in the temperature of the distilled fatty acids is achieved with the help of the distillate cooler.
As the level inside the distiller column increases, the fatty acids from the bottom of the column are pumped into the residue falling film evaporator, which are then fed back to the distiller column. With an increase in the level of falling film evaporator, the accumulated residue is then discharged, is conveyed to residue storage, after proper cooling in the residue cooler,.
Advantages of Falling Film Technology for Pre-run and Distillation of Fatty Acids: The pre-run improves the quality of the distilled fatty acids by getting rid of low molecular weight fatty acids, odorous materials and coloring compounds. The evaporation takes place inside the tubes from a thin liquid film, usually less than 1 mm in thickness, resulting in good mass transfer with minimum pressure drop. The device requires only small effective volumes, as the tube wall is heated immediately. The formation of the film takes place under the influence of gravitational force. Heating is achieved by a falling film evaporator, where highly effective heat transfer is obtained with very short liquid hold-up times in the tube. Falling film evaporators need minimum maintenance and are best for heat sensitive fatty acids. The unique design of the plant makes the process totally reliable.
5 TONS per day EDIBLE OIL REFINERY
Process Description: For refining the oil, there are three basic processes in the refinery. First process is neutralizing the oil in the neutralizer, to remove the Free Fatty Acids (FFA) by adding caustic soda. Oil is heated up to about 60oC, by thermic fluid coils and oil is stirred by stirrer. Soap stock formed due to chemical reaction is allowed to settle at the bottom of the neutralizer, from where Soap stock is taken out into soap pan.
Neutralized oil is drawn into the second vessel called bleacher, where color of oil is removed by bleaching process with the aid of chemicals such as carbon black and bleaching earth. Oil is generally heated up to 110oC by thermic fluid coils. Stirring is also continued. Bleaching process is done under vacuum.
Bleached oil then goes to the filter press where bleaching earth and chemicals are separated and clean bleached oil is then drawn to deodorizer where oil is heated above 110oC through thermic fluid coils and then live steam is purged into the oil from the bottom steam nozzles and temperature of oil is raised up to 200oC to 220oC through thermic fluid coils. Thus smell is removed from the oil in the deodorizer. Oil then goes to cooler, where water circulating in coils, take away heat and oil is cooled. Oil then goes to second filter press, where completely refined and transparent colorless oil is obtained.
Thermic Fluid Boiler, Vacuum Pump, Barometric Condenser, Catchalls, Steam Generator etc. play their role in the refining process. So these equipments are part of the refinery and connected with the vessels through pipelines.
Additional Process for palm oil refinery: Specially for palm oil refinery, fractionation process is required, in which palm olene and palm sterene are separated by scientifically cooling the refined palm oil, by chilling plant and then filtering the oil. For this purpose crystallizing vessel is used, in which chilling pipe coils cool the oil for fractionation. Palm sterene crystals are formed, due to chilling, which are separated in the filter press and pure liquid of palm olene is obtained and palm sterene cake is retained in the filter press.
UN Number for Coconut Oil : 1363
UN Number for Seed Cake: 1386
Hazard Class: 4.2
Specifications of Refinery: Capacity 5 tons per day, 4 batches of 1,250 kilograms each.
(1) All the main vessels, two neutralizers, one bleacher and one deodorizer are properly arranged on the first floor of the steel structure. All these vessels hang on the steel structure. Just below the two neutralizers, two soap pans rest on the ground floor in which soap stock is collected. There is a steam pipe arrangement in the soap pans.
(2) Steel structure has size of 14 feet x 14 feet (4.25 meters x 4.25 meters). First floor is 9 feet above the ground level. There are 8 columns of double channel, which supports the entire steel structure. It has a staircase and railing on all the sides of steel structure, at the first floor and also on staircase. Two filter presses are also accommodated on the first floor of the steel structure.
(3) Two oil tanks, raw oil tank and bleached oil tank are accommodated under the structure on the ground floor. The cooler, thermic fluid boiler, two steam generators, vacuum pump, water pumps, oil pumps and refined oil tank are arranged on the ground floor around the steel structure, outside the 14 feet x 14 feet steel structure. So total space occupied is about 30 feet × 30 feet (9 meters x 9meters).
(4) 40 feet tower is erected just near the deodorizer and its complete structure is supported from the ground floor. It is attached with the refinery structure. Barometric condenser is arranged at 40 feet height to create proper vacuum.
(5) All types of pipelines are interconnected as per the requirement of the refinery i.e. oil (yellow), vacuum (blue), steam (black), water (white), thermic fluid (red). At all appropriate places, proper valves are provided in the pipelines.
(6) Neutralizer is provided with thermic fluid coil for heating the oil.
(7) Bleacher is provided with double pipe coil coolers. One is for thermic fluid and another is for cooling water.
(8) Deodorizer is provided with a pipe coil. In the coil, thermic fluid is circulated. Steam is ejected from the stainless steel nozzles provided on the steam pipe, cross supported at the bottom.
(9) Cooler is provided with pipe coil, which circulates cooling water.
(10) In every vessel, temperature gauge is provided. Vacuum gauge is provided on deodorizer, bleacher and cooler.
(11) Neutralizer is open on the top having conical bottom.
(12) Bleacher has dished ends on both the sides. Similarly deodorizer has dished ends on both the sides. Cooler has also dished ends on both the sides.
Specification of Refinery with fractionation Process:
(13) There will be chilling plant for fractionation process, which will include shell and tube chiller, compressor, motor, pump, condenser, control panel box etc.
(14) Crystallizing unit, which is similar to neutralizer complete with chilling coil.
(15) Filter press for separation of palm olein and palm sterene.
SOLVENT EXTRACTION PLANT
CAPACITY 200 TONS / 24 HOURS
Main Solvent Extraction Plant: Equipment and accessories required for Solvent Extraction Line (Within Battery Limits) suitable for processing 200 Tons / 24 hours of pre-pressed oil cake containing less than 8 to 9% oil.
1) Preparatory Equipment for Oil Cake: Preparatory equipment suitable for preparing the cake, suitable for the further extraction process, complete with drive, panel and electrical accessories as detailed out in specification. Normally not recommended for pre-pressed cake.
2) Main Equipment: Main equipment for solvent extraction line, comprising of feeding conveyor, extractor, solvent tight conveyor, distillation tower, outgoing conveyor condensers, distillation equipment, recuperation equipment, and other related equipment as detailed out in specification.
3) Pump Sets: Pump sets comprising of Cast Iron centrifugal pumps, designed for handling solvent / miscella / oil at required duty conditions, heavy duty for continuous operation complete with flameproof motors, coupling and base frame with mechanical seals, on strategic pumps as detailed out in specification.
4) Drives: Drives for main equipment viz. Conveyors, extractor, distillation tower, recuperator complete with flameproof motors, gearbox, couplings. Special couplings are required for extractor and distillation tower drive with pulley / sprockets, belt / chain, base frames and guard as detailed out in specification.
5) Piping Materials: All required piping material within battery limit of the plant for circulation of water, steam, oil, miscella and solvent, comprising of pipes, bends, flanges, gaskets, viewing glasses, vacuum gauges, and compound gauges and temperature gauges. All required valves for water, oil, miscella, steam and solvent lines, steam traps, steam fittings.
6) Electrical Accessories: All required electrical accessories within battery limits of solvent plant, comprising of main panel board with mimic diagram, interlocking systems, indicating lights, fitted with ammeters, voltmeters in vermin proof construction. Flame proof push buttons, safety switches, rotary switches, cables connecting panel to individual motors and push buttons, are also required. Equipment lights and main plant general lights (fluorescent) in flameproof construction. Miscellaneous items like connectors, earthing material etc. as detailed out in specification are also required.
Auxiliaries: Supporting Steel Structure: Supporting steel structure for main plant complete with columns, floor beams, purlins, pent roof, trusses, base plates, one steel staircase, railings, required nuts and bolts, and steel flooring and painting for the structure. Supporting structure for hydrator and platform around it (bagging section) is provided. Supporting structure for preparatory equipment with platform. (Oil Cake)
Cooling Arrangement for Deoiled Cake: Cooling Arrangement for Deoiled Cake comprises of hood on the outgoing conveyor, blower, fan, rotary valve, cyclone, drive for blower and rotary valve, ducting connecting hood, cyclone and blower. In case of small capacity plants a suitably designed hood on the conveyor would be adequate and no blower / cyclone / ducting will be required.
Cooling Arrangement for incoming conveyor: Cooling Arrangement for incoming conveyor is required when rice bran pellets or Soya flakes are to be processed. This arrangement would cool or crip the pellets or flakes as these are being sent for extraction. Equipment similar to the one described in serial no. 2 above.
Storage Tanks:
a) Oil Storage Tanks, 40 Tons (2 Nos.) : Oil storage tanks in knocked down condition, suitable to hold 40 tons of oil each, are erected on site. Pump set complete with pump, motor, coupling and base frame. Piping for the tanks complete with valves to connect Oil Storage Tanks to solvent plant (approximately 30 meters away). Painting for the tanks.
b) Solvent Storage Tanks 25,000 liters (2 Nos.) : Solvent storage tanks in knocked down condition are erected on site. These are complete with clamps and turn buckles, for holding in place, suitable to hold 25,000 liters each. Pump set complete with pump, explosion proof motor, coupling and base frame. Piping for connecting the tanks with main plant, with valves, safety tyros valve and feed pipe.
Cooling Water and Circulation System: Cooling Water and Circulation System comprises of induced draft, cooling tower made of treated wood, complete with fan and drive. Pump set for circulating the water complete with motor, base plate and coupling with a stand by pump set for water circulation.
Piping: Piping material for connecting the Solvent Extraction Plant to water cooling pump sets complete with valves approximately 20 meters.
Electrical accessories: These comprise of panel board, cables and required electrical material.
Glass wool / Mineral wool insulation materials.
Painting: General painting material for equipment and piping. Special solvent resistance paint material including coal tar epoxy paint for internal of extractor and miscella tank.
|
|